CASE / Proterra
Proterra built two new plants with a focus on flexible material handling.
FlexQube developed material handling carts designed explicitly for Proterra’s needs. One of the key factors was to have the design harmonize with the Proterra brand.
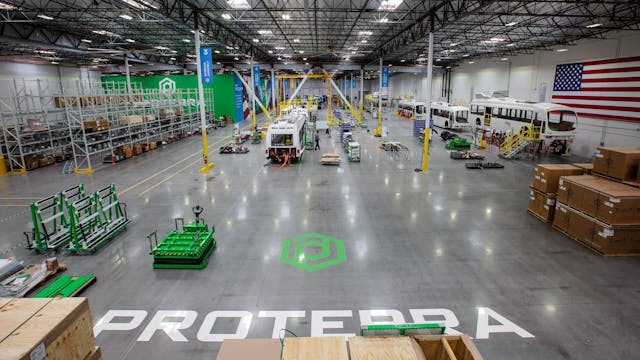
Challenge
Achievement
Solution
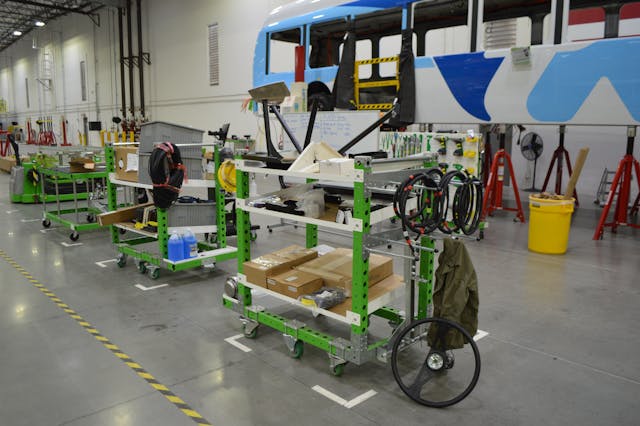
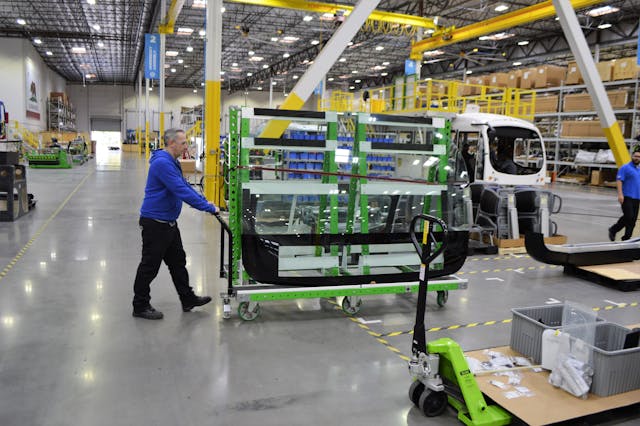
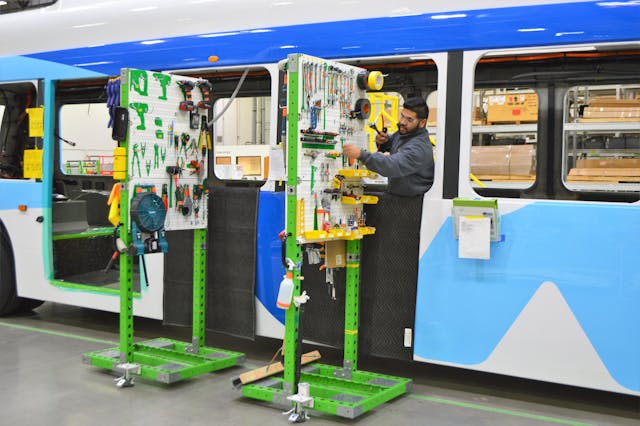
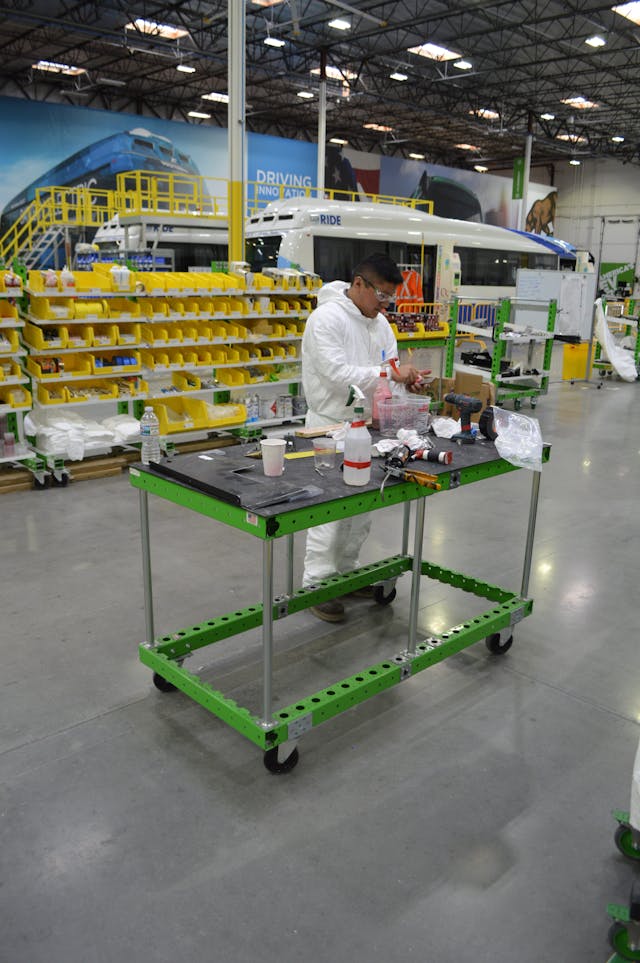
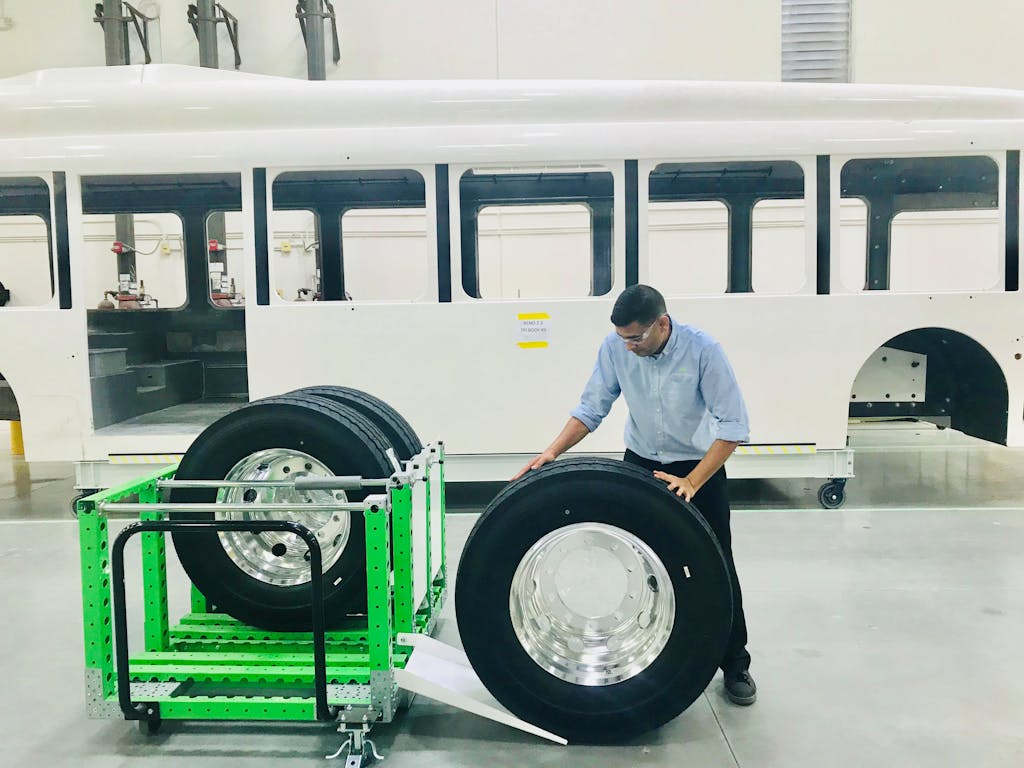
Reducing the number of forklifts paved the way for a more efficient assembly process
FlexQube developed 25 different applications for transportation and presentation of components for the assembling of Proterra’s buses. The size of the initial project made the use of FlexQube’s unique, web-based DesignOnDemand™ a vital tool throughout the process. Within these online meetings, the client is deeply involved in the creation of the carts and this created a very smooth design process throughout the project. In the end, carts were designed for tires, batteries, windshields, tools, hoses, and cables. In the end, reducing the number of forklifts used in the facilities in favor of cart-based material handling paved the way for a much more efficient assembly process.
“SEAMLESS AND TRANSPARENT PROCESS FROM DESIGN TO IMPLEMENTATION”
– Lalit Savalia, Proterra
Modification of carts
Shortly after the delivery of the initial carts, Proterra realized they already needed to modify the carts. It was a bonus that modification is in the very DNA of the FlexQube concept. Again using our DesignOnDemand™, Proterra was able to alter their carts on-site with new building blocks swiftly.
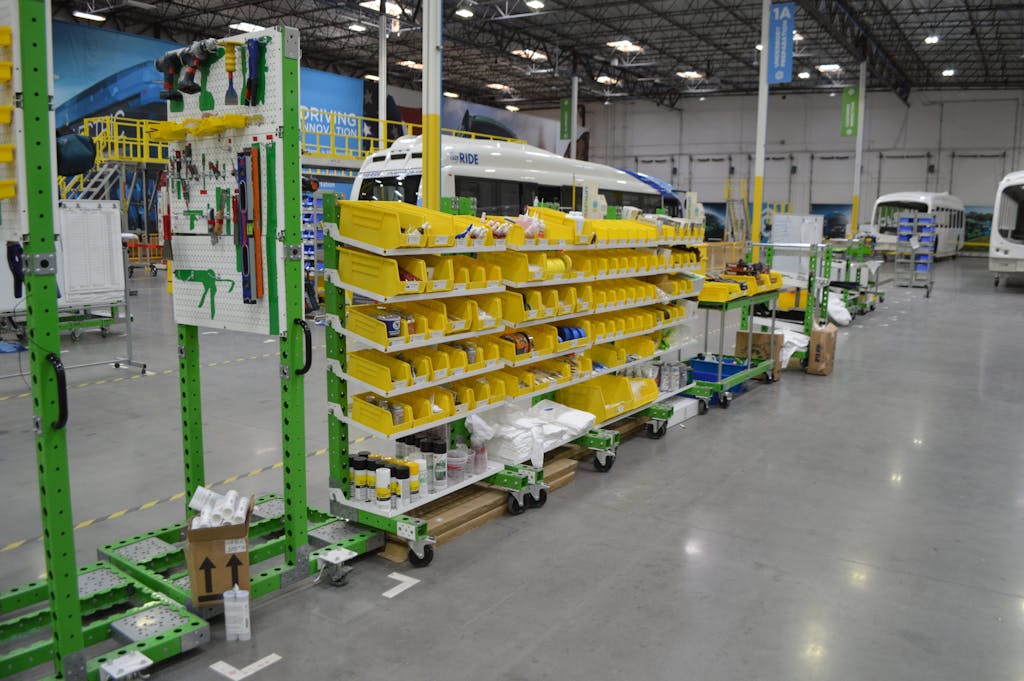