Warum muss Sicherheitskleidung getragen werden?
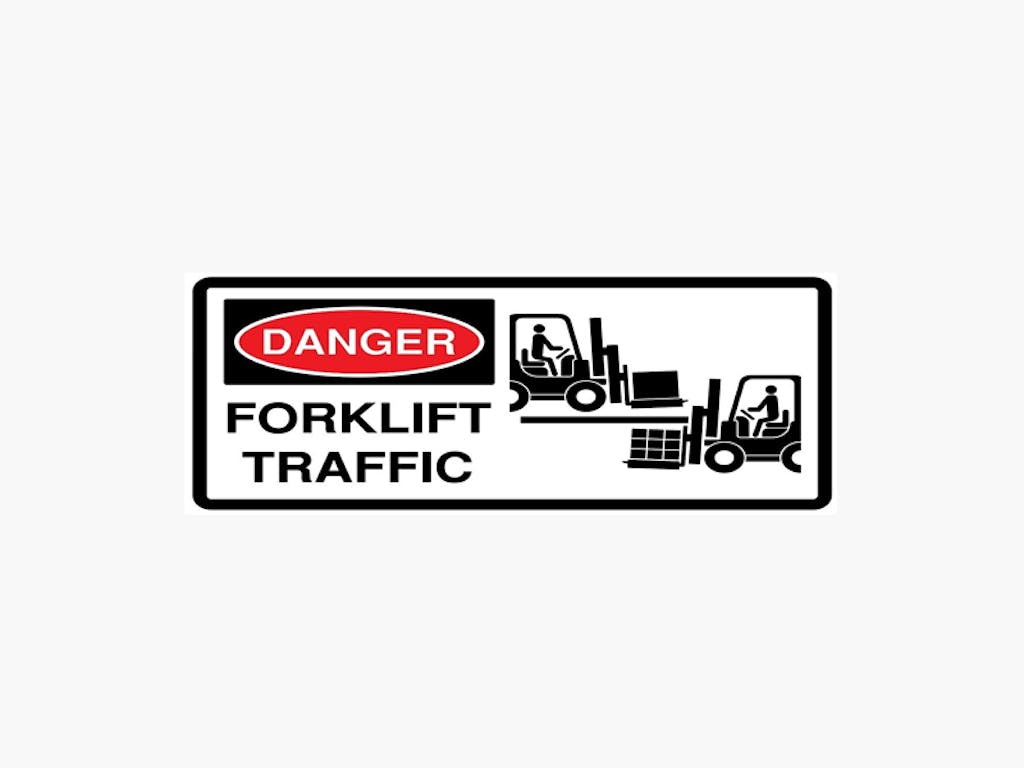
Waren Sie schon einmal in einer Fertigungsanlage? Nachdem Sie sich als Besucher am Empfang registriert haben, werden Sie vor Betreten von Fertigungs- bzw. Lagerhallen mit den Sicherheitsvorschriften vertraut gemacht – häufig in Form eines Videos. Während des vergangenen Jahrzehnts bin ich in vielen Produktionsanlagen gewesen bin, tatsächlich manchmal bis zu 15 innerhalb einer einzigen Woche. Ich schätze, dass sich die Gesamtzahl an Produktionsstätten, die ich die letzten 10 Jahre betreten habe, auf mehr als 1.000 beläuft. Folglich habe ich einige dieser Sicherheitsvideos gesehen.
Etwas, was darin niemals ausgelassen wird, sind Informationen zu Gabelstaplern.
„Achtung Gabelstapler“
„Stellen Sie sicher, Augenkontakt mit dem Fahrer herzustellen, bevor Sie einen Gang durchqueren“
„Denken Sie daran: Wenn Sie den Fahrer nicht sehen können, kann der Fahrer Sie ebenfalls nicht sehen.“
Es ist nicht so abwegig, gerade dieses Thema in Sicherheitsvideos hervorzuheben, da es allein in den USA jedes Jahr zu fast 100 Todesfällen führt und auch mehr als 35.000 Unfälle mit Personenschäden pro Jahr verursacht.
Trotzdem nutzt selbst 2019 noch die große Mehrheit an produzierenden Unternehmen, die ich besuche, Gabelstapler als primäres Element zum Transport von Waren und Material innerhalb des Fertigungsbetriebes.
Und ich spreche hier nicht von Lagerhäusern sowie Wareneingangs- und -ausgangsbereichen. Überall sind viele hupende Gabelstapler zu sehen, die an Kreuzungen anhalten, um Menschen von einer Seite zur anderen gehen zu lassen, während Sie sich ihren Weg aus dem Fertigungsbereich bahnen oder hin und her fahren. Ziemlich häufig mit leeren Gabeln und einer scheinbar unklaren Mission. Oftmals sind auch hintereinander stehende Gabelstapler in einem engen Gang zu sehen, die darauf warten, dass der vorderste seine Arbeit fertigstellt. Dabei wird nur eine einzige Palette bewegt.
Gabelstapler sind eine tolle Erfindung für viele Unternehmungen, nicht zuletzt für Andockvorgänge, das Be- und Entladen von LKW oder den Einlagerungsprozess in Lagerhäusern. Der Name spricht für sich; Gabel-STAPLER (sind zum Stapeln da).
Für die Mehrheit aller Fertigungsprozesse ist die Nutzung von Gabelstaplern zur Bewegung von Materialien aus einem Lager oder vom Zusammenstellungsprozess zur Montage oder Produktionslinie jedoch nur der Beweis für unwirtschaftliche Arbeitsabläufe, das Gegenteil von schlanker Produktion (Lean Management). Der Gabelstapler überlebt das Jahr 2019 in der Art von Unternehmen, in denen Planung und Produktion so schlecht ausgeführt werden, dass der Gabelstapler aus Gründen der „Flexibilität“ gebraucht wird. Wenn in einem solchen Werk sämtliche Prozesse und Durchlaufzeiten, einschließlich der Zulieferkette, bekannt wären, könnte der Bedarf an Gabelstaplern für den internen Materialfluss beseitigt werden.
Ich glaube, dass die Hürden zur Überwindung der Herausforderungen bei der Implementation Gabelstapler-freier Fertigungsvorgänge auf drei Hauptaspekte eingegrenzt werden können:
Eine starke Führung mit einer zukunftsorientierten Unternehmenskultur
Anwendung einer Lean Manufacturing Philosophie (schlanke Produktion)
Ein Geschäftsszenario, das alle möglichen positiven Effekte der Reduzierung der Anzahl an Gabelstaplern berücksichtigt
Die Führung
Leider ist das Fehlen einer klaren Vision und einer futuristischen Denkweise oft ein entscheidendes Hindernis für viele Gabelstapler-freie Projekte. Viele Führungskräfte sehen neue Methoden und Arbeitsweisen als ein potentielles Risiko und nicht als Chance. Selbstverständlich beinhaltet jedes Projekt mit dem große Chancen zur Verbesserung verbunden sind, auch ein gewisses Risiko. Ansonsten wäre es viel zu einfach. Der Weg zur Perfektion könnte steinig werden, doch getreu dem FlexQube-Mantra „Veränderung ist die einzige Konstante“ wissen wir alle, dass der aktuelle Status Quo keine Option ist. Die Verantwortung für die langfristige Entwicklung eines Unternehmens liegt stets beim Management. Wenn die Verantwortlichen auf dieser Ebene nicht bereit sind, ein gewisses Risiko einzugehen und Chancen zu nutzen, wer wäre es sonst innerhalb eines Unternehmens?
Lean Manufacturing Philosophie
Das menschliche Gehirn ist sehr einfach auszutricksen. Etwas, das sich schneller bewegt, wird stets als effizienter wahrgenommen als etwas, das langsamer läuft. Ein schnell fahrender, aber leerer Gabelstapler, wird leicht als produktiver betrachtet, als ein sehr langsam laufender, doch voll automatisierter Routenzug, der ohne Fahrer sechs Wagen zieht. Die meisten Menschen, die in Managementprozesse involviert sind, sind sich der verschiedenen Verschwendungen, gegen die Lean Manufacturing vorgeht, sehr bewusst. Dennoch nutzen sehr wenige Fakten und (Kenn-)Zahlen, um Verbesserungsprozesse voranzutreiben. Während viele Unternehmen den Fokus auf das Beseitigen von Überproduktion und Verschwendung, den Lagerbestand betreffend, legen, um damit Cashflow verfügbar zu machen, fokussieren sich nur wenige auf Wartezeiten, Bewegungsabläufe (von Menschen) oder den Transport (von Produkten/Material). Meiner Meinung nach sind, um es ganz deutlich zu sagen, zu viele Menschen mit einem Wirtschaftsabschluss statt einem Ingenieursstudium auf den Management-Positionen.
Betriebswirtschaftlich ausgebildete Personen neigen dazu, sich auf die Verschwendung zu konzentrieren, die hauptsächlich einen Einfluss auf Cashflow und Working Capital (Umlaufvermögen) hat. Ein wachsendes Lager oder zusätzliche Verarbeitungsprozesse (sowie mangelnde Übereinstimmungen) werden ihren Weg zu den höchsten Ebenen des Unternehmens und in die Bücher der Buchhalter finden. Ein leerer Gabelstapler wird das nicht.
Personen mit einem Ingenieurs-Hintergrund müssen einen Schritt voran gehen und auf weniger sichtbare existierende Unwirtschaftlichkeiten hinweisen. Es erfordert Erfahrung und Ausbildung in Fertigungsvorgängen, um in der Lage zu sein, zu erkennen, wenn Mitarbeiter doppelt so viele Schritte laufen, wie eigentlich erforderlich, sowie für das Umplanen des Materialflusses zur Reduktion zurückzulegender Strecken. Um Chancen in diesem Feld einfach zu identifizieren, können ein Notizblock und eine Uhr genutzt werden: Gehen Sie hinaus in den Fertigungsbereich mit einem Notizblock, der drei Spalten aufweist.
Erste Spalte: Wertschöpfend
Zweite Spalte: Nicht wertschöpfend, aber notwendig
Dritte Spalte: Nicht wertschöpfend (Verschwendung)
Dann folgen Sie einem Gabelstapler oder einem Mitarbeiter und studieren Sie in 20 Sekunden-Abständen, was dieser tut. Schreiben Sie ein Stichwort zur Tätigkeit an der jeweiligen 20-Sekunden-Marke und setzen Sie eine Markierung in einer der drei Spalten. Tun Sie das für 15 Minuten und addieren Sie die Anzahl an Markierungen in jeder Spalte (für eine 15-minütige Studie sollten es insgesamt 45 sein). Teilen Sie die Zahl in jeder Spalte durch 45, um einen Prozentanteil zu erhalten. Sie werden überrascht sein, was Sie herausfinden. Das wird Ihnen Potentiale für Verbesserung aufzeigen.
In einem nächsten Schritt können Sie dieses einfache Modell tiefer nutzen, indem Sie die tatsächlich jeweilig ausgeführte Aktivität in defr betreffenden Spalte aufführen. Für Materialtransporttätigkeiten könnte es etwas schwierig erscheinen, tatsächlich zu bestimmen, was die wertschöpfende Arbeit ist, da Materialtransport grundsätzlich als nicht wertschöpfend betrachtet wird (zweifelsohne jedoch notwendig ist).
Doch wenn wir einen bestimmten Vorgang betrachten, bspw. das Liefern von Materialwagen zur Fertigungslinie, besteht die Produktivität aus drei Dingen: Methode/Art – Leistung/Ausführung – Nutzung/Auslastung
Produktivität ist das Ergebnis, das Sie durch die Multiplikation aller drei Faktoren erhalten:
Methode x Leistung x Auslastung
Es ist sehr wichtig, daran zu denken, dass der absolut wichtigste Teil der Gleichung die Methode ist. Im Fall des Materialtransports könnte die Methode beispielsweise wie folgt lauten:
Wagen händisch aus dem Lager schieben
Wagen per Gabelstapler aus dem Lager bewegen
Wagen per Routenzug aus dem Lager bringen
Es ist einfach zu verstehen, dass die Produktivität enorm ansteigt, wenn im Vergleich zur Bewegung von Hand (1.), ein Gabelstapler (2.) diese Aufgabe übernimmt (besonders wenn wir über eine lange Distanz sprechen). Und ein ähnlich großer Unterschied kann erzielt werden, wenn der Warentransport durch einen Routenzug (3.) übernommen wird und nicht durch einen Gabelstapler (da diese Methode jetzt das Bewegen mehrfacher Ladungen zur gleichen Zeit ermöglicht).
Auslastung ist der zweitwichtigste Faktor in der Gleichung. In diesem Fall würde ich sagen, es ist die tatsächliche Zeit, die benötigt wird, um Waren/Güter vom Lager zur Fertigungslinie zu bringen. Durch schlechte Planung der Materiallieferung oder schlecht geplante Routen sowie nicht optimierte Losgrößen (um dem Tempo der Linie selbst zu entsprechen), könnte der Auslastungsgrad definitiv dramatisch gesenkt werden.
Der dritte und ganz klar der Faktor mit dem geringsten Einfluss ist der Leistungsfaktor. Interessanterweise glauben viele, dass dies etwas ist, was großen Einfluss auf Produktivität hat. Die Leistung wäre die Geschwindigkeit, mit der Gabelstapler oder Routenzug betrieben werden.
Ein Anwendungsfall
Gängige Zahlen für die Kosten eines Gabelstapler-Fahrers, die ich erhalte, reichen von 35.000,- bis hin zu 60.000,- US-Dollar jährlich (sehr davon abhängig, inwieweit die Unternehmen bereit sind, Kosten für Personalsuche, das Anlernen, die m² für Pausenbereiche etc. mit einzuberechnen). Die Kosten für einen Gabelstapler liegen üblicherweise bei etwa 10.000,- US-Dollar pro Jahr.
Insgesamt entsprechen die Kosten für einen Zwei-Schicht-Betrieb für einen Gabelstapler demnach ca.
$ 100.000,- (zwei Fahrer x 45.000,- plus den Gabelstapler mit 10.000,- USD).
Die Alternativen sind:
- Einen Menschen die Wagen schieben lassen
- Einen Routenzug verwenden
- Eine halbautomatische oder vollautomatische Lösung nutzen
Mit einer Routenzug-Lösung können möglicherweise vier bis sechs Ladungen zur gleichen Zeit bewegt werden. Das hängt im Regelfall von der Gang-Breite (Spuren und Sicherheit) ab, aber auch von der Effizienz eines zu langen Zuges, bei dem der Fahrer zum letzten Wagen hin und zurück laufen muss, um das Material zur Linie zu liefern.
Diverse Fallstudien, die FlexQube mit Kunden durchgeführt hat, zeigen einen Produktivitätszuwachs von 25-50 % im Vergleich zur Verwendung von Gabelstaplern.
Übliche Ansatzpunkte sind:
- Reduzierte Gesamt-Fahrtstrecke (da ein Zug mehr Einheiten transportieren kann)
- Verbesserte Sicherheit
- Weniger Wartezeit (weniger Verkehr)
- Verbesserte Qualität (kein beschädigtes Material)
- Verbesserte Arbeitsumgebung (weniger laut und bessere Luftqualität)
- Verwendung von Wagen ermöglicht besserer Materialpräsentation. Dies wiederum steigert die Produktivität der Arbeiter
Wo anfangen?
Man beginnt mit dem einfachsten Ablauf:
Welches Material ist aktuell das am häufigsten und längsten per Gabelstapler transportierte?
Welches Material ist eher leicht und wäre für eine Person ohne Probleme von einem Arbeitsplatz weg oder zu einem Arbeitsplatz hin zu bewegen?
Welche Person (die heute Gabelstapler fährt) wäre am ehesten offen für eine Veränderung der Aufgaben?
Wenn möglich, versuchen Sie einen Bereich auszuwählen, in dem die Materiallieferung etwas von der Hauptmontage-Linie unabhängig ist. Zum Beispiel die Materiallieferung zu einer Kommissionier- oder Bereitstellungszone. In vielen Unternehmen werden sogenannte Supermärkte zum Downsizing von Material genutzt, bevor es zur Montagelinie geht. Vielleicht wäre der Transport von Paletten und Waren in einen solchen Bereich ein guter Anfang.
Zusammenfassung
Die meisten Anlagen haben einen sehr gewissenhaften Ansatz zur Sicherheit für ihre Angestellten und Besucher. Sätze wie: „Sicherheit geht vor“ oder „Sicherheit ist unsere oberste Priorität“ sind an den Wänden zu lesen, bevor Produktionsgebäude oder -stätten betreten werden. Als Besucher muss man mit Sicherheitsschuhen, Sicherheitsbrillen, Ohrstöpseln und manchmal langen Ärmeln ausgerüstet sein oder sogar Ringe und anderen Schmuck ablegen.
Ich glaube, vielen Werkleitern fehlt ein wichtiges Teil des Puzzles. Statt zu versuchen, die Angestellten und Besucher vor allen potentiellen Risiken und Gefahren im Werk zu schützen, wäre es nicht besser, sich darauf zu fokussieren, die Notwendigkeit von Sicherheitsausrüstung durch Eliminieren gefährlicher Ausrüstung und Bestandteile zu minimieren?
Ich freue mich wirklich darauf, ein Werk zu besuchen, in der ich einfach ohne jegliche Sicherheitsausrüstung herumlaufen kann und immer noch sicherer wäre, als wäre ich draußen auf der Straße.
Geschäftsführer, Anders Fogelberg
Über FlexQube
FlexQube ist ein bewährter Partner für Gabelstapler-freie Projekte, der innovative, einzigartige und patentierte Materialfluss-Konzepte nutzt, bei denen Wagen und Regale verschraubt statt verschweißt werden. Auf Basis eines flexiblen Systems weniger standardisierter Komponenten entwickelt das Unternehmen industrielle Materialtransportanwendungen wie Palettenwagen, Regalwagen, Kit-Carts, Werkzeugwagen und Routenzüge.
Ganz im Sinne des Lean Manufacturings können mit den FlexQube-Modulen kostengünstig sichere und ergonomische Arbeitsumgebungen für wechselnde Montage- und Kommissionierungsprozesse geschaffen werden. FlexQube kann viele Jahre erfolgreicher und bedeutender Gabelstapler-freier Projektinstallationen vorweisen. In 22 Ländern nutzen Unternehmen der Branchen Automobilindustrie, Maschinen- und Anlagenbau, Logistik, Konsumgüter, Energie, Verteidigung und Medizin die Intralogistiklösungen von FlexQube.
Zusätzlich zu mechanischen Bausteinen zur Erstellung maßgeschneiderter und robuster Lösungen für Industrieanwendungen vertreibt FlexQube auch die hochmoderne Routenzug-Lösung von LR Intralogistik, den Liftrunner® Mutter-Tochter-Zug sowie die von FlexQube entwickelte autonome Lösung namens eQart®. Kontaktieren Sie uns unter sales@flexqube.com
Contact us
-
Deutschland