A Comprehensive Guide to Setting Up a Lean Manufacturing Layout on a Budget
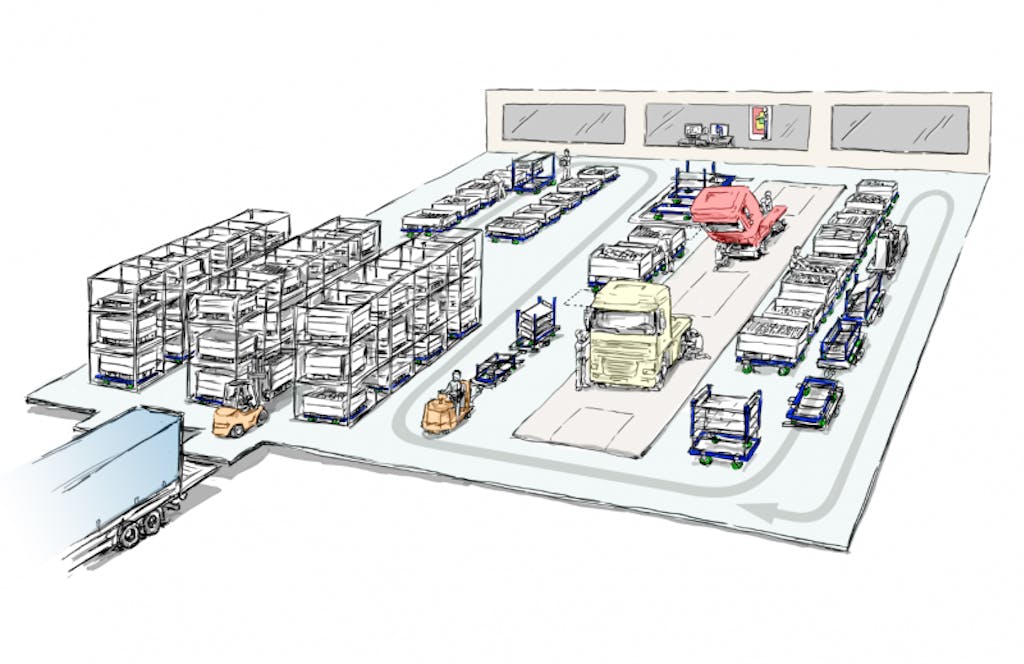
For many SMEs in the manufacturing space, early profits are generally little as one struggles to establish a brand in this competitive industry. Thus, maximizing profits by eliminating waste is an important objective for most small and medium scale production facility. Thankfully, the tricks to working with little, meeting demands, and eliminating waste have already been hacked. In this comprehensive guide, the tricks to setting up a lean manufacturing facility on a budget will be outlined for your reading pleasure.
The 5 Steps to Creating a Lean Manufacturing Factory on A Budget
Before going into details, it is important to note that there are two approaches to setting up a lean manufacturing factory and they include the Brownfield or Greenfield approach. The Greenfield approach involves starting the entire process from scratch and building the factory in a new site, as well as using new tools. The Brownfield approach involves enhancing the old site by integrating new ideas, tools, and software to achieve a lean production process. Since SMEs work within limited budgets, the steps outlined here follow the Brownfield approach to lean manufacturing.
Get the Right People
Going lean requires expertise to pull off and having the right staff makes it easier. The set up process should be handled by an experienced project manager who can evaluate the strengths and weaknesses of the old system. This includes evaluating the existing shop floor layout, available equipment, and staff competency. Therefore, your core team should consist of the facility manager, a senior level machine operator, and a representative of your workforce.
In this stage, your task is centered on getting everyone on the same page and preparing them for the task ahead. The core team will be able to provide valuable input for creating the layout for your lean manufacturing facility.
Develop Layout Proposals
The next step is developing a layout for the proposed changes in the facility. The layout must take into consideration: navigation pathways, workstation docks, storage spaces, and material handling equipment. Here again, the support of your core team has a role to play in designing a working plan.
The plan must also include risk and safety assessments, the preliminary expenditure profile. This determines the budget that will be required to execute the lean factory plans. If the layout plans are over the specified budget, the plan should be fine-tuned until it meets the required spending profile.
Analyze the Flow of the Layout
Before kick-starting any brick and mortar changes, the designed layout must be tested to see if it works. There are two ways to accomplish this and they involved the use of a computer-aided design (CAD) software application or developing cardboard models of the layout plan. This model gives you the opportunity to simulate how the shop floor will function during production. If a CAD software app is used, you could simulate how increased customer demand and other external factors can affect the lean environment.
Once this step is successfully completed, you can then access the initial plan again and make any necessary changes to it. This takes us to the next step; analyzing the transportation system in the facility.
Define a Material Handling Process
The ability to meet customer demand and production timelines depend on how materials are moved across the shop floor. An optimal lean manufacturing process should ensure materials are moved safely, handled without damage, and are defect free. This is why a transportation system is a key consideration.
Integrating the use of a Tugger train can help you meet the requirements above but it could be expensive to execute. If a Tugger train blows your budget out of the water, then swivel carts, pallets, and other material handling equipment with wheels can be used as alternatives.
Safety Considerations
With your plans in place, the final step is to ensure the entire process is safe for everyone. So, a lean facility must include machinery and equipment that have fail-safe buttons, and features that protect its users. Pedestrians and workers should also be taught about the safety policies and regulations around the facility. This will reduce the possibility of random accidents happening in your facilities.