A Guide to Tugger AGVs & AMRs – Key Things to Know Before Investing
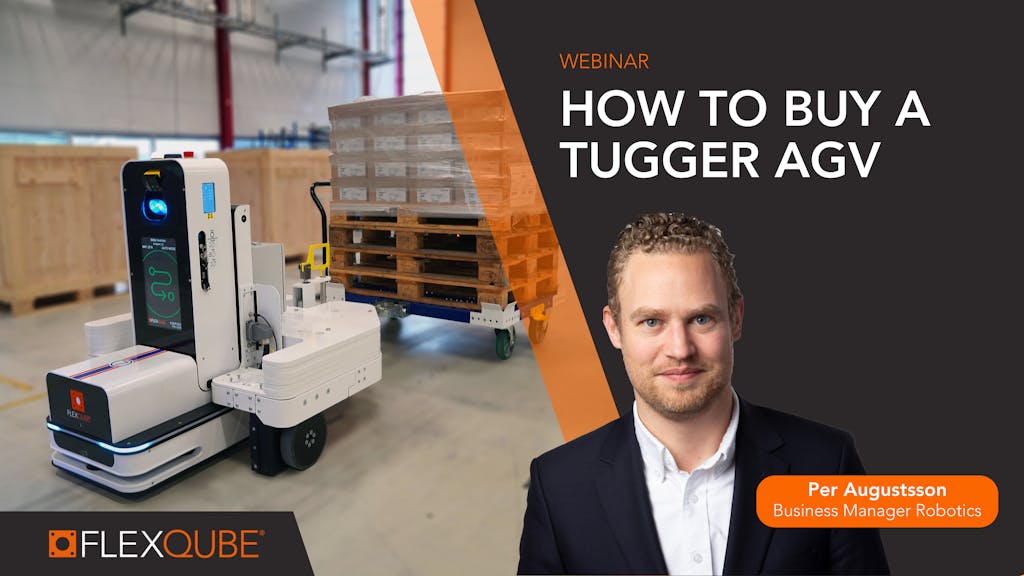
In today’s industrial landscape, the demand for smarter, more efficient material handling solutions is growing rapidly. Manual tow trucks have long been a reliable choice for moving large volumes of parts or stock in warehouses and plants. However, with challenges in recruiting forklift- and tugger drivers and the need to allocate staff to higher-value tasks, automation is becoming essential.
Enter tugger AGVs and AMRs—sophisticated automated guided vehicles designed to revolutionize traditional towing operations. These cutting-edge machines not only automate repetitive transport tasks but also enhance efficiency, reduce costs, and reshape material flow in modern facilities.
Join us at our webinar on the 23rd of January where FlexQube together with the industry experts Bluebotics, MasterMover and Bastian Solutions will discuss how the AGV market is developing, how it works and key factors when investing in Tugger AGVs.
Save you spot – SIGN UP NOW
(FlexQube Navigator AMR with Towing Load Carrier)
Industry Insights and Benefits.
Tugger AGVs, or Tugger AMRs, are commonly utilized in industries like manufacturing and logistics, where efficient transport of materials over long distances within facilities is essential. These automated vehicles are valued for their ability to streamline operations, boost efficiency, lower costs, and improve workplace safety. As a result, more companies are turning to Tugger AGVs or AMRs to automate towing processes, replacing traditional manual equipment to free up operators for more productive tasks while automating repetitive ones.
Milk runs are an example of a process that manufacturers can benefit from automating. This involves a predefined loop with designated areas for loading and unloading materials, which can be done by a forklift or manually if using totes. Since milk runs already have a clearly defined process, it remains consistent when transitioning from a manual system to an automated towing solution.
With the capability to tow multiple carts simultaneously, Tugger AGVs and AMRs offer a cost-effective solution, helping businesses achieve a strong return on investment.
The FlexQube AMR System and how it works.
1. Payload Information
The FlexQube AMR system consists of a single robot that integrates with a range of load carriers, making it adaptable to various payloads depending on the specific use case. Common loads include pallets, racks, material kits, and totes, particularly in applications where automation is viable with typical payload capacity required is between 2,000 and 3,000 kg.
2. Connecting Tugger to Loads, Navigation and Safety Systems
Our tugger AMR, which we call the Navigator AMR Tugger, is unique in the market with a standardized and patented coupling that can automatically couple and uncouple from a full train set. The system is based on a modular ‘one robot/multi-carrier’ concept, where the AMR itself is a non-load carrying system – equipped with a navigation system, safety system and battery – which couples with the motorized load carrier.
The navigation system operates in a mixed-traffic environment without the need for any physical guidance on the floor and uses advanced navigation technologies to autonomously move through environments. Sensors, camera-based vision and mapping are used to allow the AMR to navigate dynamically and to avoid obstacles in real-time. In addition, different payload dimensions require customized safety fields to ensure proper navigation and collision avoidance, as larger or irregularly shaped loads need extended or differently shaped safety zones which is a unique feature on the market.
With advanced safety systems and an advanced fleet management system, the Navigator AMR can respond to its environment and the traffic around it to ensure it delivers materials to the right place, at the right time, in a safe manner. If there are obstacles that interfere with its route, the safety system triggers the AGV to slow down or stop until the object is removed to ensure high safety for other traffic and operators.
3. Comissioning
When integrating the Tugger AMR, it’s crucial to consider the layout of the routes to ensure there’s enough space for optimized tracking of the carts in the train, allowing them to navigate curves and follow the AMR’s path. Additionally, the process of loading and unloading material onto the carts needs attention, as this will often require manual handling unless rollers are used.
In terms of floor quality, towing is a relatively forgiving method for moving material, but careful planning of the AMR’s routes is essential, especially since the robot cannot reverse while carrying a load. The best approach is to automate routes that are currently served by manual tuggers, particularly those that are used for transporting large volumes of material over long distances.
4. Investing in Tugger AGVs and AMR’s
When investing in a tugger AMR, there are several key factors to consider to ensure the system aligns with your operational needs and business goals. These factors include:
- Payload Capacity
Understanding the payload capacity is essential to ensure the AMR can handle the materials you need to transport. Tugger AMRs can often tow multiple carts at once, which increases efficiency and reduces the number of units needed for operations. The right payload capacity will depend on the size and weight of the materials in your facility.
- Flexibility and Versatility
The ability of a tugger AMR to adapt to various environments and payloads is crucial. A versatile AMR can handle different types of loads, from pallets to totes, and can navigate through diverse environments, such as tight aisles or varying floor conditions. This flexibility helps future-proof your investment as your operational needs evolve.
- Navigation System
The navigation system is a critical component, as it dictates how the AMR moves through the workspace. Factors to consider include whether the system uses Lidar, cameras, magnetic strips, or a combination of these technologies. The AMR should be able to navigate complex routes autonomously, avoiding obstacles and efficiently following predefined paths, even in a mixed-traffic environment.
- Safety Features
Safety is a top priority when automating material handling processes. Look for an AMR with advanced safety features like collision avoidance, emergency stop systems, and customized safety fields based on payload dimensions. These safety features protect workers and other equipment, ensuring that the system can operate efficiently in high-traffic environments.
- Return on Investment (ROI) From a financial perspective, towing with an AMR offers strong ROI potential. Since a single AMR can tow multiple carts simultaneously, this significantly reduces the need for human labor and increases operational efficiency. Depending on the use case and the number of shifts in operation, ROI can be realized in as little as 12-15 months. On average, most businesses can expect an ROI within 24 months, which is highly acceptable considering the increased safety, flexibility, and efficiency that tugger AMRs provide.
By carefully evaluating these factors, businesses can make an informed decision that maximizes the benefits of automation and aligns with long-term operational goals.
WEBINAR
Don’t miss out – hear from industry experts and learn more about Tugger AGVs and Automation!