The Comprehensive Guide to Agile Manufacturing
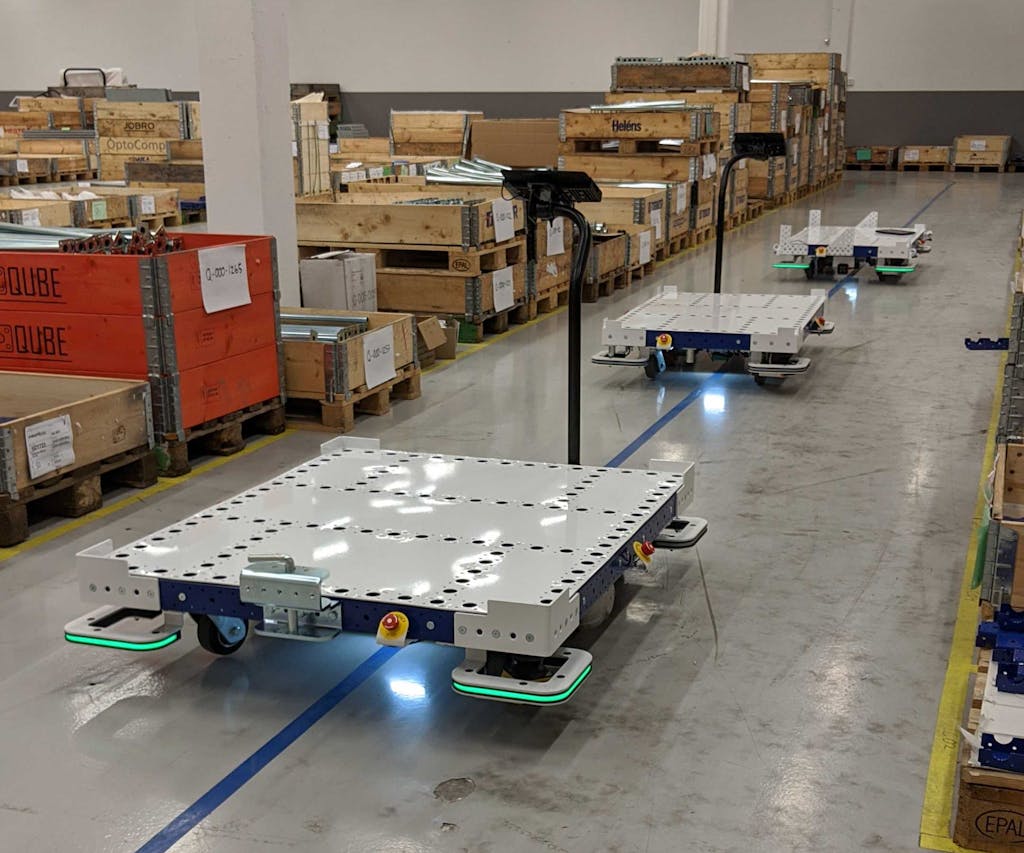
If the occurrences of 2020 have taught us anything, it’s that disruptions that can shut down the global industrial sector can happen in the blink of an eye.
Although pandemics are unusual events, the manufacturing industry faces disruptive forces regularly. These disruptive events may include increased customer demands, a disrupted supply chain, unplanned machine downtime, or staff shortages.
The aforementioned disruptive forces are not mere conjecture. The World Economic Forum stated that the pandemic had affected global supply chains, which reduced manufacturers’ ability to meet demand. The manufacturing sector is also expected to deal with extensive demand backlogs as vaccines are taken, and a semblance of normality is reached. Lastly, Ever Given’s blockade of the Suez Canal, which lasted for two weeks and stopped material supply, highlights the need for contingency plans in Manufacturing.
Agile Manufacturing has since been described as a means for manufacturing organizations to handle disruptions while ensuring that throughput quality is not affected. This guide will serve as a roadmap for implementing agile manufacturing strategies to meet an increasingly changing world.
What is Agile Manufacturing?
Agile Manufacturing is defined as an organization’s ability to respond to change factors in real-time without reducing throughput quality or going over a specified budget. As described earlier, these change factors could be a changing market situation, demand fluctuation, trade wars, or even a pandemic.
Agile Manufacturing is generally seen as the next step every manufacturing organization must take after successfully implementing lean manufacturing strategies. Thus, cutting down on waste is the first step to optimizing manufacturing resources, while the ability to respond to real-time disruptive forces is the second step to delivering sustainable revenue growth.
Although a healthy bottom line is good for every business, improving customer-service levels by consistently meeting demand with quality products grows a brand that generates revenue. Agile Manufacturing makes achieving a healthy bottom line and delivering high service levels possible.
Implementing agile Manufacturing requires the use of certain tools to develop strategies and to train manufacturing personnel about applying these strategies. The tools that support agile manufacturing processes can be broadly classified as manufacturing support technologies or digital transformation technologies.
Digital Transformation Technologies and Agile Manufacturing
Digital transformation technologies are the tools organizations use to replace manual processes and physical items with digital ones. The digital transformation of the manufacturing industry provides manufacturers with ready tools to design and implement agile manufacturing strategies.
The digital transformation technologies the manufacturing industry can rely on and currently relies on include both hardware and software tools. Edge computing hardware such as IoT and smart devices are examples of hardware solutions, while cloud computing, edge software, and the industrial cloud are software solutions.
Digital transformation solutions enable manufacturers to capture essential data from the factory floor. These data sets provide the ability to understand the performance of manufacturing equipment and even predict customer behavior. Capturing accurate data from the shop floor is the backbone of agile Manufacturing because it provides the basic information digital transformation solutions thrive on.
For example, when increased demand is expected, a manufacturer must consider its facility’s capacity to produce items to meet the new demand. To evaluate its facility’s production capacity, simulation modeling software can be used to answer ‘what-if’ questions. The accuracy of the answers gotten from the simulation model depends on the accuracy of the data sets used to build the model. Thus, capturing inaccurate data leads to inaccurate agile manufacturing strategies.
Digital transformation solutions also provide the tools to analyze future trends which is an essential aspect of agile Manufacturing. Gaining insight into future disruptive factors ensure manufacturers can respond better to change. The use of demand forecasting tools and resource allocation solutions means manufacturers can gain insight into increasing customer demand based on historical data. The forecasted information can then be used to develop capacity plans and allocate resources to meet changing requirements.
Evaluation tools are not the only digital transformation solutions required to develop and implement agile manufacturing strategies. A flexible material handling system is also needed to deliver materials just-in-time to service workstations. Automated mobile robots and automated guided vehicles with the ability to adapt to changes when transporting materials ensure raw materials get to where they are required despite unexpected changes. Automated mobile robots (AMRs), for example, bring complete autonomy to the material handling process. When unplanned downtime occurs due to a defective machine, AMRs can take decisions in real-time to quickly provide working stations with the materials they need.
The Roadmap to Developing an Agile Manufacturing Strategy
To implement a functional agile manufacturing strategy, manufacturers must have a road map to approach the implementation process. These four steps can help you get started with developing an optimized road map:
1. Research
Implementing agile Manufacturing starts with understanding the different factors associated with implementation. These factors include choosing the perfect technology partner, deciding on the material handling system to utilize, building a team, and the cost of implementation. Questions such as the ones below could help you get started with your research:
- How much will it cost to purchase or subscribe to the digital transformation solutions that make agile manufacturing work?
- Do we have the working personnel to handle the agile system once put in place?
- How do you convince C-level managers to come on board with the implementation process and provide a budget for it?
- How do I find the right technology to support the implementation process?
The answers to these questions can kick-start the strategizing process and developing an executable plan that works.
2. Assemble a Team
Agile manufacturing processes must be sustained to ensure that they can be applied anytime changes or disruptions come up. Thus, a team to implement and sustain the developed strategy is required. It is also important to consider the possibility of individuals handling multiple roles when implementing an agile strategy. For example, an operator with multiple skillsets may be required to handle multiple tasks when staffing challenges occur.
3. Choose a Technology Partner
Choosing the right digital transformation solutions partner to implement agile manufacturing strategies is important to achieving your goals. Technology partners support the implementation process by helping manufacturers plug manufacturing equipment into data collection devices, configure automated material handling systems, as well as other technical support. Choosing the right partners starts with asking the right questions such as these:
- Does the technology supplier have a track record of servicing manufacturing outfit like yours?
- What after-sales support does the technology provider offer its clients?
- Can a demonstration workshop using your manufacturing data be developed?
4. Implement with Continuous Progress in Mind
Agile Manufacturing is an iterative process where constant innovation is needed to adequately navigate through change. Thus technology solutions should be modular to accommodate new solutions or any changes to continue to provide sustainability agility.
Agile Manufacturing Best Practices
A successful implementation starts with coopting everyone to be on board with agile Manufacturing. Thus, proper communication and collaboration between operators on the shop floor are required which is why implementation best practices are needed. The four best practices to have in mind include:
- Enabling an interconnected system – Successful agile manufacturing plans take into consideration every aspect of the manufacturing process, from customer demand to getting the product to customers. Thus, digital transformation initiatives should connect the manufacturing operators, inventory, human resources, and customer support to achieve agility.
- Highly Trained Workforce – The skill level of operators plays an important role in utilizing digital transformation tools and responding to changes in real-time. Although the roadmap highlighted earlier covers assembling a team, that team must consist of individuals comfortable with applying digital transformation technology. Manufacturers can choose to fill any skill gaps by hiring skilled technicians.
- Customer Focused Product Design – An agile manufacturing system revolves around the customer and should be able to meet fluctuating customer demand without reducing the quality of the product produced. Communicating with the customer to provide accountability and make them part of the process ensures products that meet customer expectations are manufactured.
The Benefits of Agile Manufacturing
The benefit agile manufacturing brings is in its definition; the ability to respond to change without affecting product quality…but other benefits exist. These value-added advantages include:
- Increases consumer satisfaction levels – With the advent of e-commerce, 90% of customers view quick delivery as a defining factor when making purchases. The ability to meet customer demand within a specified delivery timeline leads to happy customers who will consider becoming long-term consumers.
- Supports customization – Varying customer requirements mean manufacturers may have to optimize discrete manufacturing facilities to produce customized items. Agile Manufacturing supports the customization of items to meet these demands.
- Supports lean Manufacturing – The digital transformation technologies that enable agile Manufacturing also support lean manufacturing initiatives. Implementing a responsive process reduces material waste and optimizes resource allocation when dealing with change.
Conclusion
Like all disciplines, implementing agile Manufacturing requires gathering proper knowledge of the subject. This guide provides insight into the process and a road map to get started. It also recommends further reading into the technologies and the material handling systems that support agility. With this knowledge, you can apply agile Manufacturing across your organization and reap its benefits.