Tips From FlexQube’s Design Manager
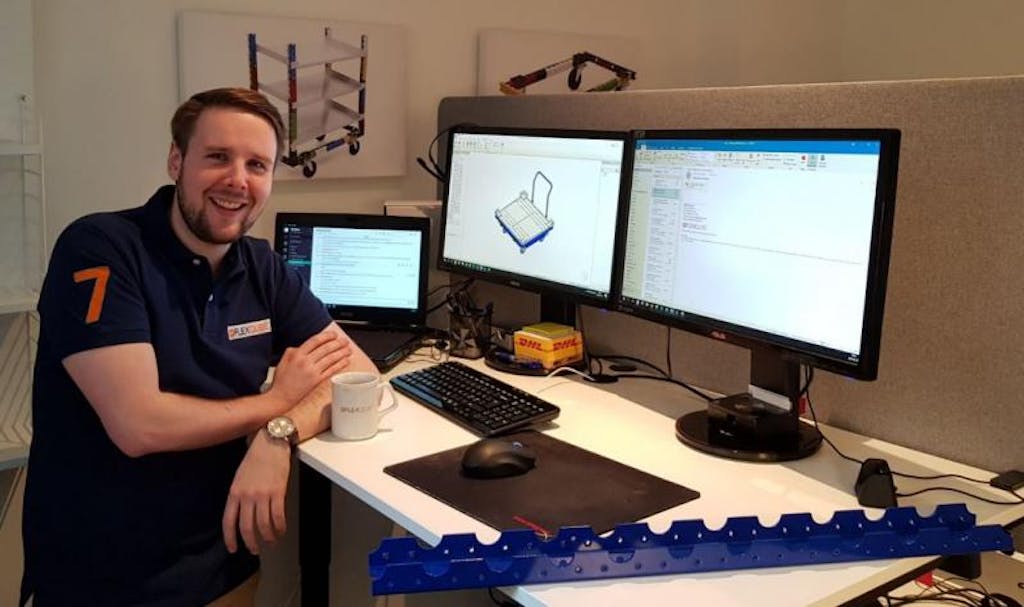
1. Nice to have vs Need to have
Before starting the process of a design decide which functions you need to have and which functions would be nice to have. In the end, it’s usually a trade-off between price and function.
2. Prepare!
Before starting the process of a design thoroughly investigate the specs and limitations for the project. Generally the later a problem or requirement is discovered the more costly it gets. However, since FlexQube offers a modular concept it makes it a little bit less painful!
3. Don’t rush it
Start on time and plan, rushed projects often lead to mistakes, which can be costly in the future.
4. CAD files
Have an odd looking part or something that needs to be placed in a very specific way? Look into if you have CAD files of the part, that way we can try it out directly in the model and make sure it works!
5. Check out our Solutions Library
Before heading into a DesignOnDemand meeting check out our Solutions Library! Here you can find all of our previous designs. Maybe we have already designed the cart you’re looking for, perhaps two can be mixed and to fit your needs! It will also give you a better understanding of what we do here at FlexQube and what it is possible to create with our building blocks.
If you’re interested in joing FlexQube for a DesignonDemand™ session visit https://flexqube.outgrow.us/ENG-DoD-Preparation
You may also like: