What are the Lean Manufacturing Principles?
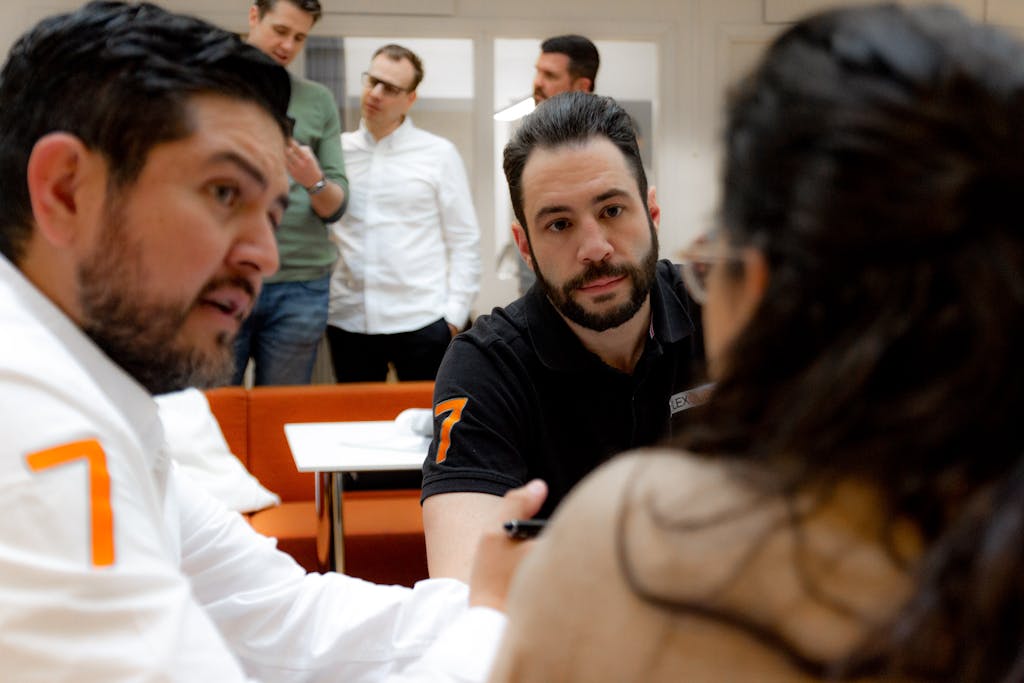
Lean manufacturing is a common term throughout manufacturing facilities, and many large companies have adopted lean manufacturing practices. It is praised as being a tool that can increase production, boost profits, cut down costs, and scale down inefficiencies within the manufacturing process.
Origins of Lean Thinking
Generally, the creation of the Toyota Production System is widely considered the initial step towards lean thinking and the lean manufacturing principles we have today. However, there are a few people and companies that stand out before this. Henry Ford had begun testing different methods of interchangeable parts and adjusting the movement of parts to try and reach a standard level of product quality. However, it is correct that Toyota revolutionized manufacturing performance after WW2 by introducing the Toyota Production System. This system had the ambition of reducing the cost of production and improving the quality of the manufactured products. Since then, the idea of lean thinking and lean manufacturing has grown into a global practice that has been defined by five fundamental principles.
The five lean manufacturing principles
Beginning with the Toyota Production System, five critical lean manufacturing principles were outlined. These five principles being:
- Identify Value
- Map the Value Stream
- Create Flow
- Establish Pull
- Pursuit of Perfection
Identify Value
Each company is created because it can bring some value to a customer’s life. This is where the lean manufacturing principles begin, with a highlight on becoming more customer-focused. To do this, an understanding and identification of what value is; is essential. This helps in understanding what your customers are willing to set aside their money for and purchase. Once you have this understanding of what your customer is willing to pay for, you can begin to eliminate functions that the customer doesn’t value. This leads to an improved manufacturing process because you start to spend time and focus on the items that generate the most value.
Map the Value Stream
Mapping the value stream is a method of creating the complete life-cycle of your products. It includes everything from the products’ design, to how the customer uses the product, all the way to how the product is disposed of. Doing this can give you a detailed timeline of steps throughout your work process. The purpose of conducting this life-cycle activity is to highlight the areas within your life cycle that bring value to your customers. On top of this, it will also be easier to find the internal actions that do not bring value to your customers. Having this value stream mapped out is a big step forward in prioritizing which areas of the business should receive focus and resources.
Create Flow
Creating flow is a critical principle in lean management because it helps in how parts, materials, or items progress from production to shipping and then to the customer. A key idea in lean thinking is eliminating waste throughout the whole manufacturing process, and waiting is a tremendous waste on the flow of the overall process. Each time an order is placed, the goal should be to establish a smooth distribution of product from you to the customer. Within this step, every aspect needs to be considered, from shipping, equipment, employees, materials, and the final delivery. All of these aspects should be considered in making sure that no bottlenecks build up and have a negative impact on the flow of goods from manufacturing to delivery.
Establish Pull
This fourth principle is closely related to the third principle, “creating a flow.” The idea behind establishing a pull is quite straightforward. A pull system means that work only begins when there is a demand or an order, and there is the capacity to complete the task. Whereas most traditional manufacturing systems are push systems, which means that they begin work before their being a demand or an order for the product. The purpose of this is to create value only when it is needed or requested by customers.
Pursuit of Perfection
This final principle is closely related to continuous improvement. The idea behind this principle is to improve all processes continually. This can include all functions, whether this is in your team, your equipment, or the process itself. This can often be seen as one of the most difficult of the above principles to complete, and different continuous improvement methods have been developed to help. For example, Plan-Do-Check-Act and the root cause analysis.
Conclusion
Implementing these principles and an overall “lean thinking” mentality can significantly improve the processes within your organization. Having a thorough understanding of the five principles mentioned in this article is an excellent start to creating a more efficient workplace. To best implement these ideas, it is best to find the right way for it to work within your processes. Taking the adoption of the lean principles in a step-by-step process and evaluating what is needed is the best approach.