Why It’s Time to Prioritize Heavy Duty Carts over Forklifts
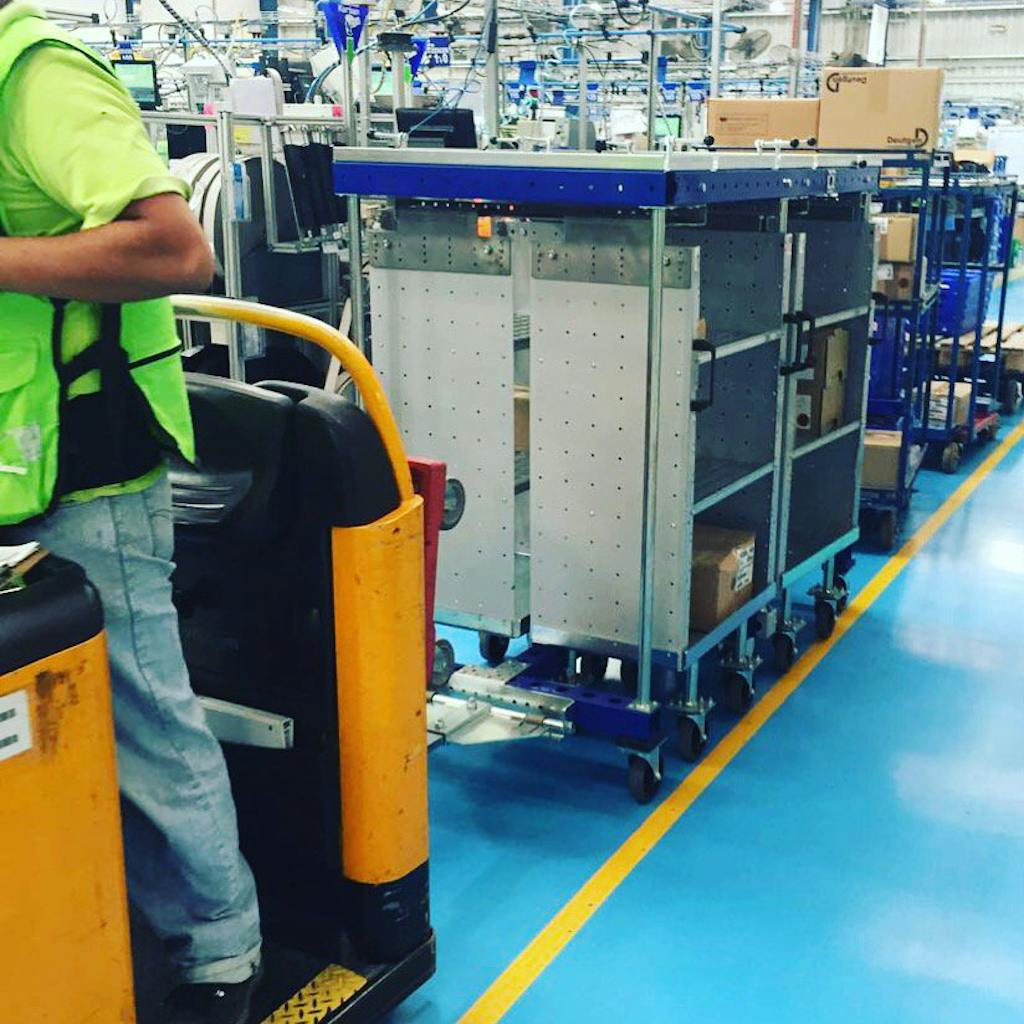
Tow Tractors with heavy duty carts are now widely used to move materials efficiently. Even companies who are hesitant to give up forklifts at first are now using tugger trucks. Both manned and unmanned trucks have proven to be more efficient, more cost effective and more productive. They are also more ergonomic and more flexible to use than the traditional forklifts.
Design
The carts are designed like trains. The main or “mother” truck is linked with multiple carts, allowing it to move multiple loads at a time. The unmanned tugger truck is designed with an automated system. It has a limited speed and pre-set route or destination. On the other hand, the manual tow tractor allows the operator to control the cart’s speed, route and destination.
Most tow tractors have a maximum capacity of 10,000 pounds. Regardless of the capacity, the number of carts that can be linked and pulled from behind the main truck is limitless.
The carts can tilt, rotate, and elevate. They can also be placed at the ideal distance and heights through rollers, cubicles and integrated spinning carousels. These ergonomic factors help to minimize the operator’s reaching, stretching, bending, and strains.
Productivity
Cesar Jimenez, who works for Toyota Material Handling, U.S.A. pointed out that a forklift can only carry up to two loads at a time. But with a tugger, multiple heavy duty carts can be pulled and moved at the same time.
Beneficial for Workers
The ergonomic design of tow tractors is beneficial to workers. With the help of tow trucks, people can move heavy carts without strain. The workers no longer experience the same fatigue they get from using forklifts. As a result, they can stay alert and productive for a longer period.
Workers are required to learn more things in using forklifts. They need to know how to pick up the load from the rack or the ground. There is a greater risk of damage if the load is not picked up properly.
Unlike forklifts, tugger trucks are easy to use so anyone can operate them. They allow more flexibility in workstations since the products can be moved from one location to another by anyone who is available. The products are also safer since the loads are simply attached to carts. The truck allows visibility for drivers. It can maneuver around tight turns and it doesn’t tip over.
Cost
The safety of heavy duty carts has a positive impact on overall productivity and cost. There are no known major accidents caused by tugger train systems. The ergonomic design also reduces injuries and musculoskeletal disorders. As a result, workers experience less fatigue and fewer injuries. There are fewer absences and lower insurance claims.
Things to Consider
Removing the cart from the train can be challenging. If the needed load is placed in between two carts, it has to be unlinked from both and dragged away. After the cart is removed, the other two carts have to be reconnected.
While the number of carts pulled behind the mother truck is limitless, it can be limited by the truck’s hauling capacity. Numerous carts can be complicated to drive if they have to travel on an inclined surface, rough road or outside the facility.
The number of carts can also be limited by a narrow path if the truck has to turn. The first two carts at the back of the mother tuck can follow the same maneuver but the third cart may turn at a slightly different radius.
If you’re looking for a similar solution, contact us at sales@flexqube.com
You may also like:
How to start the transition from forklifts to a tugger train system