Las 10 mejores herramientas Lean sugeridas.
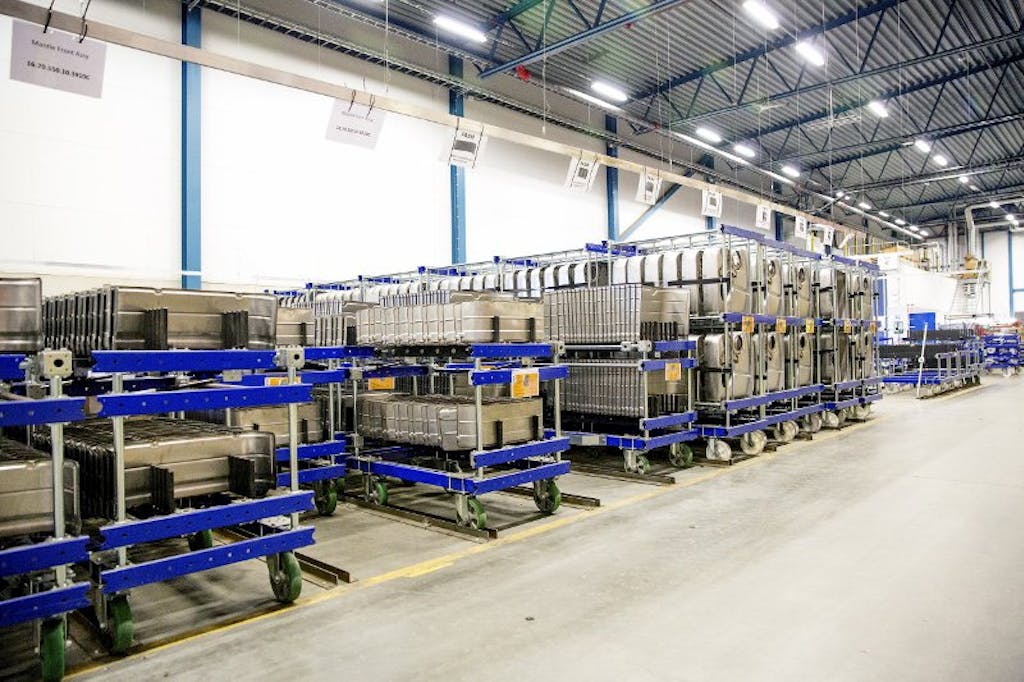
Conozca las principales herramientas de manufactura esbelta. La manufactura esbelta y sus principios son pautas fundamentales para las instalaciones de fabricación en todo el mundo.
Dentro de los principios de lean, existen herramientas específicas que se pueden implementar en diferentes momentos para contrarrestar diversos problemas. Hemos discutido varias de estas herramientas en publicaciones de blog anteriores, como el ciclo PDCA y la metodología Jidoka. Pero en esta publicación, proporcionaremos resúmenes breves de 10 de nuestras herramientas Lean sugeridas para que las implemente. Las diez herramientas que resumiremos son:
- Pokayoke
- letrero
- Seis grandes pérdidas
- Hora del tacto
- 5S
- Análisis de raíz de la causa
- Gemba
- Objetivos INTELIGENTES
- Mapeo de flujo de valor
- Análisis de cuellos de botella
repelente de póquer
Poka-Yoke tiene que ver con la detección de errores y garantizar que, si hay un error, no pase a la siguiente fase de fabricación. El objetivo de Poka Yoke es lograr una tasa de deserción cero en toda la línea de producción. Inicialmente se acuñó en Japón y surgió inicialmente como una prueba de tontos, pero luego se convirtió en una prueba de errores. Los beneficios de Poka-Yoke permiten ahorrar tiempo y dinero al limitar la cantidad de productos defectuosos hasta la siguiente etapa de la línea de fabricación.
letrero
Kanban significa letrero o tablero visual y es un sistema de tarjetas para ayudar a organizar el flujo de materiales de bienes a través de una planta de fabricación. Kanban comenzó en la década de 1940 como un sistema de planificación fácil de usar dentro de la industria automotriz de Toyota. Kanban ayuda a visualizar el proceso real de los materiales, y las tarjetas se pueden usar como un “sistema de extracción” que indica cuándo se requieren más productos. Esto puede ayudar a evitar los cuellos de botella en la línea de fabricación, así como a evitar el exceso de oferta de ciertos materiales.
Seis grandes pérdidas
Las seis grandes pérdidas son seis áreas diferentes de pérdida de productividad y eficiencia. Es un método útil para identificar de dónde provienen las pérdidas significativas y pautas sobre cómo eliminar el desperdicio. Las seis grandes pérdidas son:
- Paradas no planificadas
- Paradas planificadas
- Pequeñas paradas o ralentí
- Velocidad o ciclos lentos
- Defectos de producción
- Pérdidas de inicio
Hora del tacto
El tiempo takt puede verse como el ritmo uniforme o el tiempo de tasa que se necesita para completar un producto terminado que se puede entregar a un cliente. Se conoce ampliamente como la velocidad de producción, y esta herramienta puede ser muy beneficiosa para comprender lo que se necesita producir cada día. El Takt time se puede determinar averiguando la cantidad de tiempo de trabajo disponible durante el día dividido por la demanda del cliente de un producto en particular. Por ejemplo, si hay 420 minutos de trabajo por día y los clientes demandan 30 productos terminados por día. Entonces el tiempo takt es 420/30 = 14 minutos. Esto significa que un producto debe terminarse cada 14 minutos para satisfacer la demanda.
5S
5S es un método para organizar diferentes espacios de trabajo, de modo que estén preparados para una óptima seguridad y capacidad de trabajo. Su enfoque principal es garantizar que las herramientas, los materiales y los artículos se coloquen en las posiciones en las que deben estar, y que todo el espacio de trabajo se mantenga limpio. Los sistemas 5s incluyen los siguientes pasos:
- Clasificar
- Poner en orden
- Brillar
- Estandarizar
- Sostener
Estos cinco pasos necesarios ayudan a eliminar el desperdicio dentro de la fabricación que se puede producir en espacios de trabajo no organizados.
Análisis de raíz de la causa
El Análisis de Causa Raíz es un método de resolución de problemas que está diseñado para encontrar lo que está detrás de la causa del problema en primer lugar. Detener cualquier proceso de fabricación cada vez que se encuentra una irregularidad y luego realizar una investigación es una de las mejores formas de completar el análisis de causa raíz. Una de las formas más comunes de encontrar la causa raíz de un problema es el enfoque de los cinco por qué. Esto implica preguntar por qué cinco veces para llegar a por qué ocurrió el problema.
Gemba
Gemba es un término japonés para el “lugar real”, y esto puede referirse a alejarse de su escritorio e ir al “lugar real”. Puede usar Gemba cuando hay un problema que necesita ser resuelto o si está trabajando en un proyecto de mejora. Esto ayuda a garantizar que la resolución de problemas o las mejoras que está planeando funcionen en la realidad.
Objetivos INTELIGENTES
Los objetivos SMART ahora se utilizan en una amplia variedad de negocios y departamentos; esto solo sirve para mostrar la utilidad del método. INTELIGENTE significa:
- Específico
- Mensurable
- Alcanzable
- Importante
- Específico del tiempo
Esto puede ayudar en la planificación y elaboración de estrategias para ayudar a que las metas sean más efectivas.
Mapeo de flujo de valor
El mapeo del flujo de valor es una herramienta para ayudar a trazar el flujo del proceso de producción. Esto es beneficioso para ver una perspectiva de arriba hacia abajo del flujo de sus materiales en su línea de producción. El uso de esta herramienta puede ayudarlo a encontrar retrasos en el proceso, ineficiencias en ciertas áreas y mejoras. Un mapa de flujo de valor inicial también se puede utilizar como herramienta para delinear desarrollos futuros para la producción y dónde se pueden eliminar los desechos.
Análisis de cuellos de botella
La herramienta Análisis de cuellos de botella se usa para encontrar áreas en el proceso donde la eficiencia está restringida. Esto ayuda a los fabricantes a encontrar las áreas en las que deben centrarse para mejorar el rendimiento de la línea de fabricación. Mejorar las áreas donde hay un cuello de botella puede conducir a un mejor resultado en otras áreas del proceso.
Hemos esbozado breves resúmenes de las diez herramientas lean que creemos que podrían ser beneficiosas para su línea de fabricación. Si aún no ha comenzado con ninguno de estos, le recomendamos comenzar lentamente y elegir solo uno o dos que puedan tener un impacto significativo en su línea de fabricación. Comenzar tratando de implementar los diez al mismo tiempo podría tener efectos adversos a largo plazo, y es mejor realizar uno a la vez.
A FlexQube nos aseguramos de poder hacer uso de herramientas Lean con la frecuencia que corresponda.