Optimización de la logística de almacenamiento con robots móviles autónomos
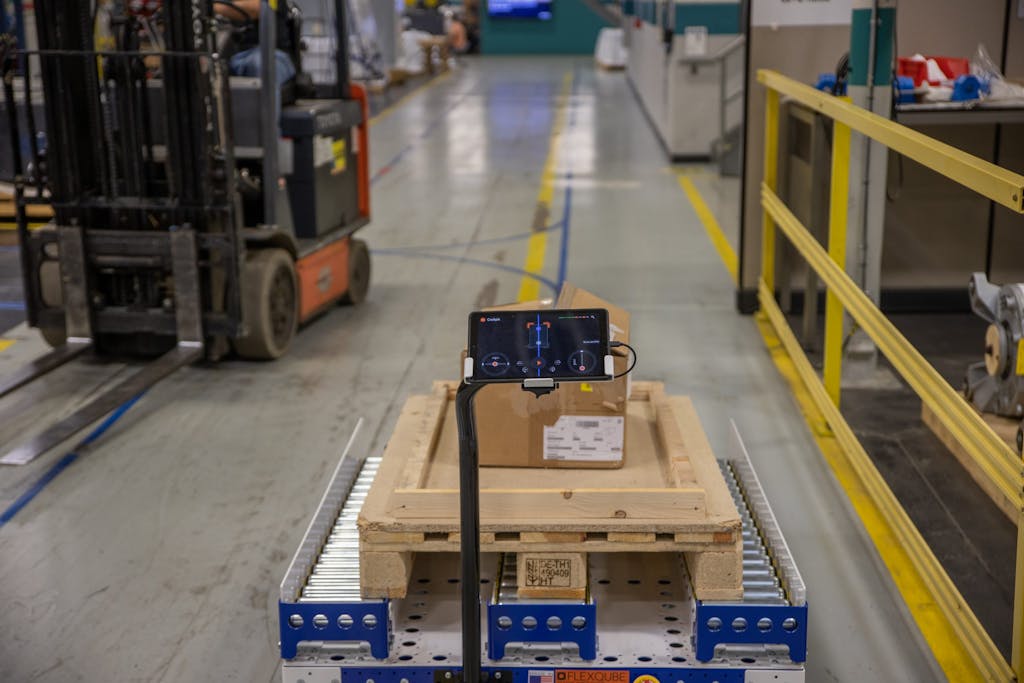
El sector industrial ha dependido continuamente de las instalaciones de almacenamiento para almacenar temporalmente mercancías para cumplir con los pedidos.
Desde la 1ª a la 4ª revolución industrial, una operación de almacén optimizada siempre ha llevado a un rápido cumplimiento de los pedidos y un ciclo de producción optimizado y una mejor gestión de inventario. Por eso algunos han llamado al almacén el faro que dirige los caóticos procesos industriales.
Un almacén organizado conduce a una mayor optimización del proceso, mientras que la desorganización conduce a niveles de servicio más bajos. Para comprender por qué la desorganización afecta la optimización de las actividades relacionadas con el almacenamiento, es necesario conocer las funciones de un almacén. Los almacenes sirven como:
- Centros de envío: un almacén de centro de envío es donde los bienes y otros artículos se almacenan y envían a otras ubicaciones. El centro de envío se encuentra tradicionalmente en regiones estratégicas a las que pueden acceder fácilmente las empresas que necesitan los productos almacenados en ellas.
- Línea de montaje: en la industria de fabricación, el inventario y otros recursos se almacenan en almacenes internos a los que se puede acceder rápidamente durante un ciclo de producción. El almacén generalmente contiene componentes fabricados o herramientas de ensamblaje que deben ensamblarse o usarse para ensamblar un producto final.
- Espacio de almacenamiento: el almacén tradicional es un espacio de almacenamiento donde se guardan los artículos hasta que se necesitan para ayudar a la producción o aumentar la disponibilidad en el mercado de un producto en particular.
Los centros de envío, el almacenamiento y los almacenes de la línea de ensamblaje deben funcionar de manera óptima para acelerar la entrega de productos y los ciclos de producción. Por lo tanto, los efectos de un almacén desorganizado repercuten en la línea de montaje y dan como resultado menores ingresos y clientes insatisfechos.
Para garantizar la optimización del almacenamiento, se requiere un sistema funcional de manipulación de materiales. El manejo de materiales se refiere al movimiento de materiales dentro de un edificio o entre un edificio y un vehículo. Por lo tanto, el almacén promedio se basa en sistemas de manejo de materiales para garantizar que los artículos guardados se transfieran correctamente cuando surja la necesidad. En el almacenamiento de la línea de montaje, se requiere el manejo de materiales para mover materiales, componentes y herramientas desde los almacenes a las estaciones de trabajo dentro de la planta de fabricación.
La optimización del almacenamiento en los centros de envío se basa en una planificación logística optimizada y los sistemas de manipulación de materiales también tienen un papel que desempeñar. La logística son los procesos involucrados en el transporte de artículos terminados o materias primas hasta el usuario final. Estos artículos se deben mover de un centro de envío a un vehículo antes de llegar al usuario. Se requiere un sistema de manejo de materiales para mover los artículos desde el centro de envío sin incurrir en daños.
Transporte de material dentro del almacén
Para facilitar el proceso de manipulación de materiales y el transporte dentro del almacén, se han desarrollado diversas estrategias de transporte a lo largo del tiempo. Estas estrategias van desde los recorridos de la leche hasta el transporte A a B, entre otras. Un resumen de las estrategias de transporte incluye:
La leche corre
Este proceso de transporte implica el movimiento de materiales o cargas desde un almacén o área de almacenamiento centralizado a diferentes secciones de una instalación. Los recorridos de leche se utilizan para dar servicio a las líneas de montaje y ejecutar entregas justo a tiempo.
Carreras A a B
Este proceso de transporte o manipulación de materiales implica el movimiento de la carga del punto A al punto B. La mano de obra y los carros o paletas se utilizan generalmente para mover cargas de un punto a otro.
Puntos de presencia en el territorio (POPITT)
POPITT se refiere a las instalaciones del almacén donde los clientes vienen a recoger productos terminados o devolver productos defectuosos. El sistema de transporte de material utilizado aquí es generalmente manual a través de carros.
La necesidad de procesos autónomos dentro del almacén
La logística en el almacén implica tres actividades principales que incluyen; procesamiento de pedidos, gestión de inventarios y transporte. El procesamiento de pedidos se basa en las solicitudes de los clientes mediante formularios de pedido. Para los vendedores de productos, como en una tienda de comercio electrónico, las solicitudes de pedido son para productos terminados, mientras que en las solicitudes de pedido de fabricación se inicia el ciclo de producción. La gestión de inventarios se refiere a la gestión de mercancías en espera de ser transportadas a los sitios de venta o al piso de montaje. El transporte implica mover los materiales solicitados a áreas específicas.
Los procesos manuales asociados con el almacenamiento y sus tres actividades conducen a errores. Por ejemplo, los formularios de pedido llenados en papel se pueden perder, y analizar el inventario disponible escrito en papel es una tarea que consume mucho tiempo y tiende a cometer errores. Por lo tanto, adoptar la automatización industrial reduce estos errores.
La industria del comercio electrónico ha dado la bienvenida al uso de tecnologías de transformación digital para automatizar los procesos de almacenamiento. Las tecnologías como el software de gestión de inventario simplifican el procesamiento de pedidos y las solicitudes de pedidos coincidentes con el inventario disponible. El modelado de programación y simulación reduce el tráfico en el taller al manipular o transportar materiales para mejorar las medidas de seguridad. A pesar de desarrollar horarios optimizados utilizando software de modelado de programación y simulación, todavía ocurren errores dentro del almacén porque los humanos proporcionan la mano de obra que impulsa el transporte de materiales.
Hoy en día, el uso de un sistema de manipulación de materiales manual es responsable de miles de accidentes en el piso de la tienda. Para eliminar la amenaza a la seguridad del operador, los almacenes deben considerar la automatización del proceso de transporte utilizando robots móviles autónomos.
Los robots móviles autónomos (AMR) son dispositivos inteligentes que pueden moverse a través de un entorno sin requerir la ayuda de un operador humano. El entorno, en este caso, es el diseño del almacén y se espera que los AMR naveguen por el piso dinámicamente sin tener que depender de una ruta fija predeterminada o pistas magnéticas.
Los AMR se basan en tecnologías avanzadas para navegar por el taller. Estas tecnologías incluyen sensores para rastrear su entorno inmediato y comprenderlo, equipo de carga y descarga para automatizar la recolección de pedidos y otros dispositivos inteligentes para capturar datos. Los AMR se diferencian de los AGV en diversas formas, pero la diferencia más importante es su capacidad para navegar por el taller sin seguir pistas preestablecidas.
Los AMR automatizan de manera integral la logística interna y el proceso de manejo de materiales dentro de las instalaciones del almacén utilizando las tecnologías mencionadas anteriormente con las que están equipados. Cuando se implementan, los AMR pueden servir como dispositivos de borde que capturan datos del almacén y transfieren los datos capturados a plataformas informáticas centralizadas para su posterior análisis.
La autonomía que proporcionan los AMR significa que se pueden implementar para manejar los recorridos de leche y otras estrategias de transporte dentro del almacén. Los AMR pueden actuar como enlace con otras herramientas de transformación digital, como el gemelo digital, para implementar algunos modelos comerciales de la Industria 4.0. Por ejemplo, un cronograma basado en riesgos integra cambios en tiempo real, como nuevos plazos para optimizar las operaciones del almacén. Los AMR pueden utilizar el nuevo cronograma para acelerar sus entregas justo a tiempo para cumplir con el nuevo cronograma de entregas.
Los beneficios de los robots móviles autónomos
El uso de AMR dentro del almacén viene con ventajas de valor agregado que conducen a un mayor crecimiento de los ingresos. Los beneficios más importantes de automatizar el manejo de materiales utilizando robots autónomos en el almacenamiento incluyen:
- Tiempos de entrega más cortos – Los almacenes más grandes significan un amplio espacio de almacenamiento con miles de inventario. Navegar por estas estructuras complejas aumenta el tiempo de espera para cumplir con los pedidos y es propenso a errores, ya que navegar manualmente por espacios grandes incluso con un mapa es un desafío. Los AMR están equipados con la capacidad de analizar datos e identificar inventarios rápidamente. La velocidad de operación que aportan los AMR reduce el tiempo de espera para cumplir con los pedidos a granel en los grandes almacenes y reduce los tiempos de caminata de los operadores dentro del almacén.
- Mayor flexibilidad – Los AMR no necesitan estar conectados para seguir rutas establecidas. Esto significa que un AMR puede encontrar su camino a pesar de los cambios recientes en el diseño de un almacén para acomodar nuevos productos. La flexibilidad que proporciona la autonomía significa que los AMR pueden encargarse de nuevas actividades sin tener que pasar por ningún proceso de incorporación complejo.
- Mayor seguridad –Una de las principales razones para implementar AMR en los almacenes es reducir los accidentes en el piso de producción causados por el tráfico y el uso de equipo de elevación pesado, como carretillas elevadoras. Los sensores integrados en los AMR garantizan que comprendan su entorno para ajustar su velocidad y evitar colisiones en tiempo real al manejar actividades de manejo de materiales. La aplicación de AMR para el transporte repetitivo también aleja a los humanos de situaciones problemáticas que pueden causar daños.
- Escalabilidad – Los AMR se pueden implementar utilizando estrategias de implementación modular que se pueden escalar para cumplir con las operaciones en expansión. El proceso de incorporación no requiere la colocación de orugas o la compra de varios carros remolcadores o equipos robóticos, lo que reduce el costo inicial para utilizar AMR. Los gerentes de almacén pueden simplemente agregar nuevos AMR a una flota disponible cuando se requiera una ampliación.
Conclusión
Los robots móviles autónomos proporcionan una flexibilidad a la gestión logística que las soluciones tradicionales de manipulación de materiales no pueden igualar. La implementación de un AMR es un movimiento para transformar digitalmente los procesos de almacenamiento mediante la integración de los aspectos de automatización de la Industria 4.0.
¡Llega a nosotros!
-
U.S.