4 Benefits of Tugger Train Systems
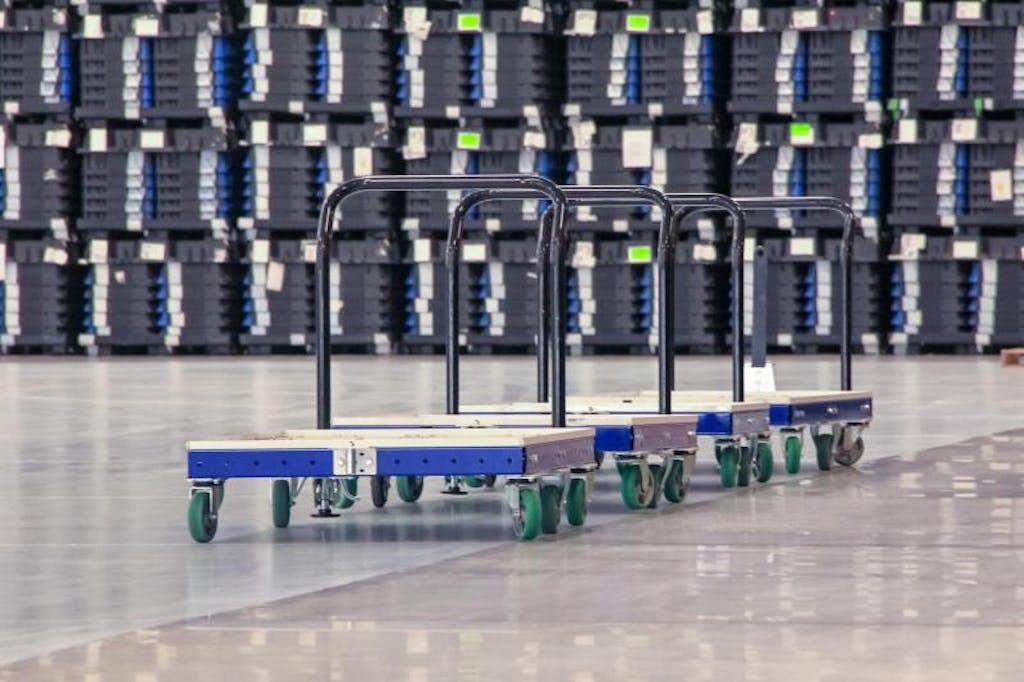
Tugger trains are small-scale transportation trains used in ferrying production materials across shop floors. Tugger trains are the preferred choice of manufacturers in the aerospace, automotive, supply, and industrial design industries. This is why:
Tugger Trains: The Four Important Advantages
Increased Supply for Discrete Manufacturing – Discrete manufacturing processes are usually employed in producing sensitive customized goods. Therefore, the materials used here must be supplied on-time and in great condition. To accomplish this, many manufacturers employ techniques that are skewed towards careful handling while overlooking supply speed. With Tugger trains, this trade-off is no longer needed.
Tugger train systems are designed or can be designed to provide adequate care with material handling while also enhancing delivery speed. This is due to the fact that Tugger carts provide more material security than other material handling techniques while these carts are transported by vehicles along set routes. The carts guarantee safety and the ability to carry many materials and the (vehicle cab) speeds up movement through the shop floor.
Reduces Floor Congestion – The shop floor has always been tagged as the engine room of most manufacturing facilities. This is due to the supply, production, packaging, and delivery activities that occur in them. Unsurprisingly, shop floors ended up becoming the most congested part of a manufacturing facility, and this leads to confusion. The integration of a Tugger train system can drastically eliminate congestion if correctly applied.
It takes only one to two persons at any giving time to load, operate, and unload a Tugger train. Don’t forget that the Tugger train system comes with specified transportation route which should be away from other traffic or machine pathways. This decongestion of the shop floors of factories also increases productivity and enhances employee safety.
Flexibility with the Changing Times – Today, lean manufacturing is making the move to Industry 4.0 where both waste and over-reliance on humans are the enemies. But the Tugger train system still lives on because Tugger trains are adaptable and can be designed to meet the material handling and transportation needs of a brave new industry.
How can this be accomplished? Through automation—another tenet of Industry 4.0—is the answer. Today, unmanned vehicles have become popular in factories such as those owned by Amazon and Alibaba. Therefore, the tugger can be automated to follow pre-set routes when delivering materials. This will lead to increased efficiency and exact delivery times. Therefore, an automated Tugger train system is clearly the future of material handling and transportation as you make the move to Industry 4.0.
Ergonomic and Economic Advantages – The design of Tugger carts is not static. This means you can adapt or choose the best cart design that simplifies the loading and unloading process for your employees. Customizing the shape, size, and material handling equipment attached to the train system also has its economic impact on the production process. This impact is a drastic reduction in what it previously cost to move materials across a shop floor.
Once material delivery and return times are predictable, this eliminates uncertainties and the financial loss that comes with unforeseen occurrences. The reduced manpower also means you can channel the excess wages to other important aspects of the production cycle.
The flexibility, customization, and certainty Tugger train systems bring to manufacturing cannot be overlooked by forward-planning manufacturers. Therefore, the time to integrate a Tugger train system in your production lines is now. You can kickstart the process by discussing your factory’s requirements with our experienced technicians today.
Contact us today if you are interested in implementing a tugger train system into your facility at sales@flexqube.com.
How to start the transition from forklifts to a tugger train system