4 Steps to Adapting Your Manufacturing Lines to Change
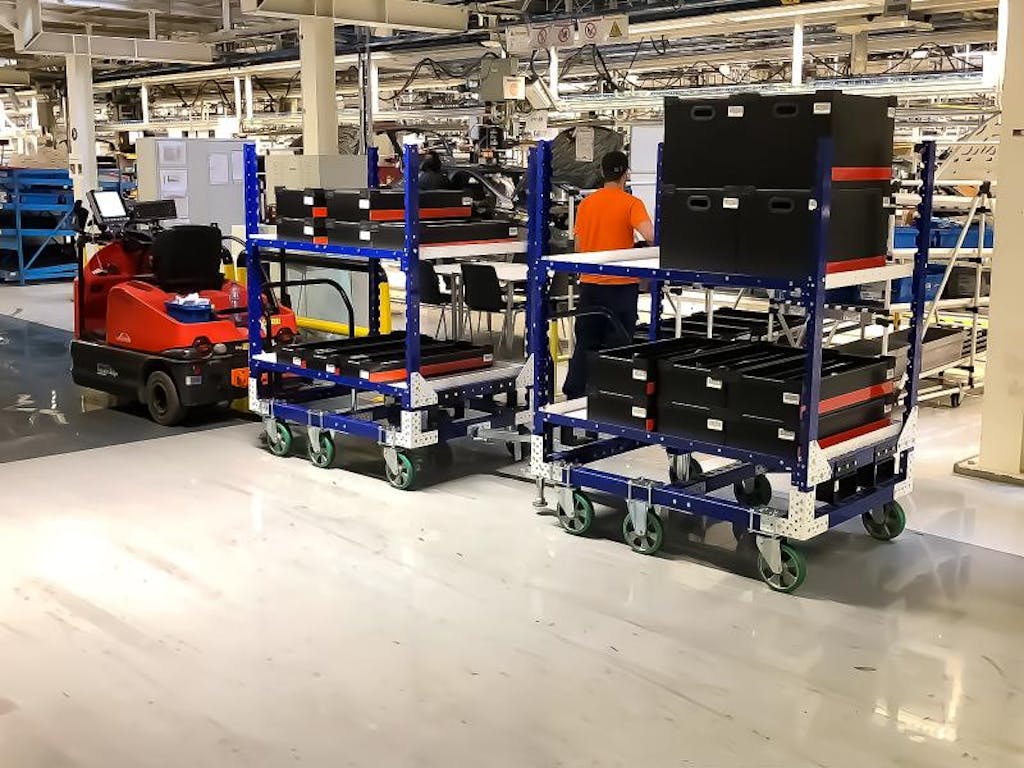
Last Updated: 5th March 2020
In 2017, UK manufacturers recorded a loss of approximately £180 billion due to problems with material handling systems or downtimes, and this was by no means an isolated incident. Statistics show that nearly 33% of businesses in the manufacturing industry also recorded losses caused by material handling inefficiencies. This is why the move to Industry 4.0, where automation becomes the order of the day, is slowly but surely gaining ground. But as the manufacturing industry continues to make a move to Industry 4.0, there are a lot of challenges industry leaders, and production managers need to come to terms with.
One of the significant challenges is the need to adapt manufacturing lines to meet Industry 4.0 standards, and what are these standards? These standards are automated production processes where manufacturing lines, material handling carts, and systems form a smart factory. In this post, the four steps to adapting your manufacturing line to meet these industrial changes will be highlighted to smoothing the transition process for manufacturers.
Step 1 – Automating the Manufacturing Line
The first step is assessing the factory space, production machines, and material handling needs to determine how each step of the production process can be automated. This is where digital transformation and the use of sensors, RFID tags, and precision module kits come into play. A centralized software application that can collect the data produced by these components in the manufacturing line will also go a long way in increasing the efficiency of the production process. One of the ways that FlexQube is looking at automating the manufacturing line is by adding automated building blocks to our carts. Adding automated blocks to our already modular system leads to the AGV System. The AGV is a smart and motorized FlexQube cart, it has motors, a battery and cameras added to a regular FlexQube cart.
Step 2 – Enhancing Material Handling and Transportation
In traditional production floors, material handling and movement are generally with the use of generic forklifts, carts, and manual transporting devices. As stated earlier, these conventional methods have been responsible for the low delivery performance and reduced quality due to damages. To manage these challenges, a new material handling process that efficiently supports the smart factory must be developed. During the design phase, the ability to attain the outlined targets should be the driving force:
- Higher delivery performance
- Increased safety and ergonomics when designing material handling equipment
- Improved communication/information link across the manufacturing line.
Once these targets have been understood, the next phase is designing the material handling equipment needed to achieve your set goals. The design process for a custom, efficient and ergonomic material handling cart includes the following;
- Defining the objectives of the cart
- Analyzing the material movement and transportation requirements
- Create multiple design options for the material handling cart
- Evaluate each design option and select the adequate option
- Implement the chosen design and train employees on proper usage.
If this process is done correctly, the results will lead to multiple benefits for the manufacturer, such as a reduction in manual transformation, transparent information sharing, employee safety, and reduced downtime. All these will increase production capacity and output substantially while ensuring product quality standards are adhered to.
Step 3 – Embracing Digital Transformation
The next step to dealing with the traditional challenges manufacturing lines face is integrating digitization to speed up production, reduce material loss, and deliver high-performing or quality products. To achieve this, devices that can collect data, increase precision levels, and automate production must either enhance traditional machines/processes or replace them.
Material handling equipment is also not left out in the digitization revolution. Carts can also be equipped with sensors to determine the weight of the equipment they carry, as well as RFID technology to track their movement. The ability to track the progress of material handling carts will simplify the transfer of information and ensure the next phase in a production line gets its material on-time.
Step 4 – Ensuring interconnectivity and Predictive Analysis
As stated in step 1, a centralized software application with the ability to collect the data produced by the different components that make up the manufacturing line is needed. This is because project automating software can provide electronic tickets that communicate the next step to take or the arrival of a material handling cart at a production post.
The data produced by an automated manufacturing line, its machines, and supporting devices can also be used to track the health of production equipment. Therefore, automated tickets that schedule the necessary maintenance activities can be produced to ensure a device is either replaced or serviced before it breaks down. This will enhance communication, increase productivity, and keep overhead expenditure at a minimum.
According to studies from PWC, 72% of manufacturers across the automotive, aerospace, industrial manufacturing, and discrete manufacturing communities will integrate Industry 4.0 process by 2020. Therefore, to remain competitive, your manufacturing lines must adapt or be left behind. At FlexQube, we can help you take the significant step of customizing your material handling equipment to meet the challenges of this new industrial age. Our experienced engineers understand the technical process of designing customized carts to satisfy your particular requirements, and the FlexQube concept allows you to embrace change and the ever-changing environment that manufacturers exist within.