5 Ways Material Handling Equipment Can Drive Growth in Automotive Facilities
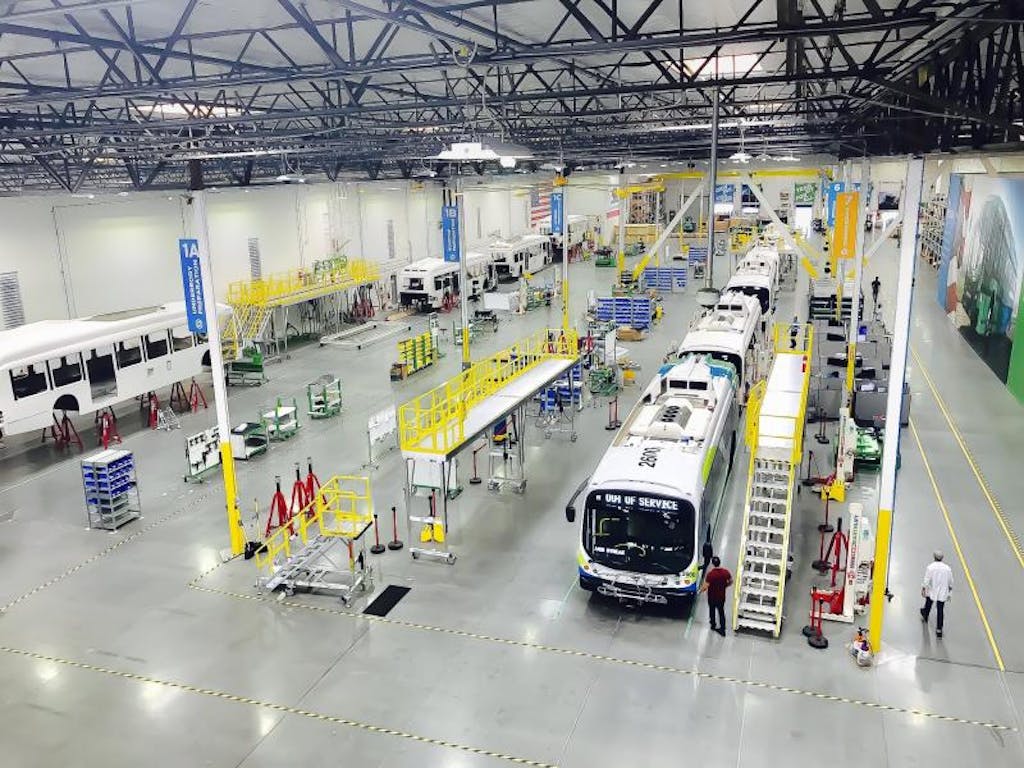
One of the reoccurring issues stakeholders in the automotive industry have always faced is that of advanced planning and scheduling during production. This is why automobile giants like Ford and other companies have overshot vehicle release dates on many occasions. To understand why this is so, one must have a first-hand understanding of the importance of planning and scheduling as well as, what an optimal scheduling process consists of. Having this knowledge is the first step to discovering how material handling equipment drives growth.
Two major operational factors drive the planning and scheduling process in automobile factories. These two production-based issues are the Master Product Scheduling (MPS) Process and the Production Activity Control (PAC) Process. The MPC is focused on the following activities:
• Developing a production schedule
• Forecasting future demands
• Adapting scheduling plans when new information is received
On the other hand, the PAC process takes into optimizing the following production-based operations.
• The timely delivery and release of materials, tools, and components
• Ensuring the needed tools are available at exact times
• Ensuring customer orders are completed within specified timeframes
Therefore an optimal planning and scheduling process in the automotive industry must solve MPC and PAC-related issues. A great MPC and PAC process is what speeds up production without reducing quality which drives growth. Also, innovative material handling equipment such as Tugger carts, flatbeds, racks have an essential role to play in planning and scheduling.
Analyzing the 5 Ways Carts Can Enhance Scheduling in Automotive Factories
Carts have essential roles to play throughout the entire process of an automobile production process. These roles include assisting the assembling, distribution, and delivery process across shop floors. Here is an outline of how carts help:
Speeding Up Component Assembly
The smaller and mid-sized products in an automobile shop floor are assembled in workstations. So these components are then transferred to conveyors where they are fixed to the vehicle. The PAC process plays a role in ensuring these components are quickly assembled according to a predetermined schedule.
Mother-Daughter cart solutions can be used to organize the different parts that make a component and deliver them to workstations. The tools to be used in these work stations can also be provided using a flow rack. The ability to customize these cart solutions is what makes them work. The flow rack or Mother-daughter cart can be personalized to fit the tools/materials to be transported.
The versatility an innovative cart provides, therefore, solves the PAC-related task of delivering tools/materials to workstations as scheduled.
Organizing Tools/Materials to Ensure Availability
The Master production scheduling process focuses on forecasting production needs. The process also ensures the tools and materials needed are available during assembly. But to know if enough materials are available, the organization is required to quantify these materials easily.
This is another crucial aspect where storage carts have a role to play. A compartment cart is just the solution needed for the organization. As these carts can be used to store smaller components like light fixtures, gear sticks and other small materials. Shelving is a boon to the automotive industry and ensures smaller parts are efficiently organized and accounted. Therefore, with the right cart, keeping track of materials and arranging workstations are made possible.
Safely Transporting Tools Across Workstations
Automotive factories make use of conveyors systems to transport larger vehicle components due to efficiency reasons. A conveyor system is faster and much more efficient than a forklift or other manual material handling equipment when transporting hundreds of car doors. However, when carrying multiple small components across workstations, another solution is needed.
A Tugger train system is excellent for transporting diverse small and mid-sized materials/tools across automotive shop floors. This is due to how innovative a Tugger train cart is. Various Tugger carts can be customized to carry and organize multiple tools and materials in one run. Therefore, with the right Tugger train system, heavier components like tyres and lighter parts like tail lights can be delivered simultaneously. Tugger train systems are also safer and need less personnel to operate. If the right release/securing mechanism is used, then one person can easily, load, manage, and offload a Tugger train.
Enhances Agile, Flexible Production
Another important issue PAC processes try to solve is meeting production timelines and customer orders. In other to do this, an agile, flexible approach to production is being adopted in automobile factories. This has led to the creation of smart, flexible automotive factories by industry stakeholders. This agile approach to production aims to eliminate waste while manufacturing according to customer’s requirements.
An example of the role customer orders play in pushing for a smart, flexible factory can be seen in this example. When 100 customers order SUV’s and 50 order electric sedans, how is production completed? It is visible that modular or linear factories will struggle with such demands. Therefore a flexible approach must be adapted to meet these orders, and a flexible factory needs flexible material handling equipment.
This is where the ability to customise carts to meet the demands of a flexible production approach is necessary. Tugger carts, flow racks and shelves can all be personalised for a smart industry. These carts can also be made autonomous or driven by a Tugger train when the need arises.
Developing a High-performing Scheduling Process
The rise of Industry 4.0 or the smart factory means almost every process in an automotive factory is supported by simulation. Therefore material handling processes must be capable of being integrated into a simulated environment. This is because they are tasked with handling the motions that occur in shop floors.
So, for a high-performing smart factory, the carts must be able to collect data, such as the number of components, speed of movement etc. This data can then be integrated into simulation systems when planning manufacturing schedules. Therefore, innovative material handling equipment with smart features is the future of the automotive factory.
Innovative carts play an essential role in the scheduling and planning processes in automotive factories. They ensure materials are delivered on time with minimal damage. This, in turn, speeds up the manufacturing process and ensures orders are delivered as promised. With the rise of smart factories, the need for more intelligent carts will increase. So for automotive manufacturers to keep their competitive edge, stakeholders must partner with material handling equipment manufacturers.
At FlexQube, we have spent the time developing innovative carts for the automotive industry. So you can leverage on our hard-earned experience to build innovative material handling solutions for your automobile factories.
If you’re looking at learning more about how flexible material handling carts can help you in your facility, contact us!
You may also like:
Some questions with our Design Manager for Mexico