7 Steps to Boost Your Performance with Lean Material Handling
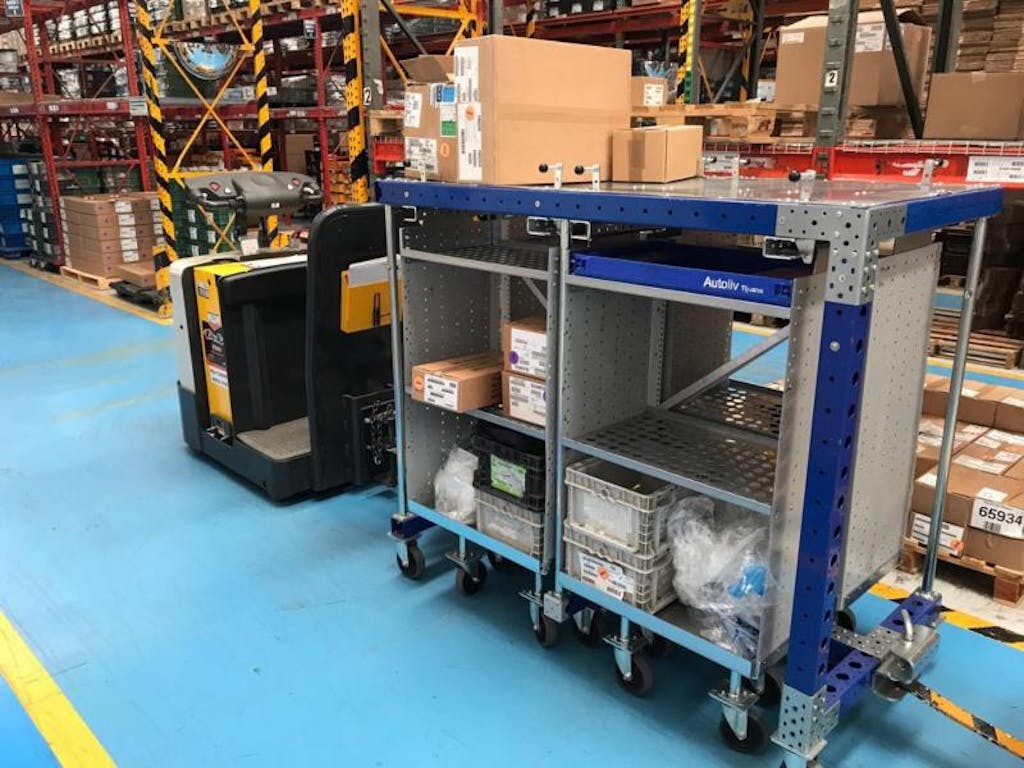
Last Updated: 11th February, 2020
Materials handling refers to the process of controlling, moving, storing, and protecting materials for consumption, manufacture, distribution, and disposal. It is a vital process because materials have to be handled properly in order for them to maintain their condition and quality, as well as reach their destination safely. Lean material handling consists of a handling system that reduces the effort, cost, and time needed to accomplish material handling procedures.
Lean material handling is preferable to the traditional material handling system, which delivers materials in an unorganized manner and causes problems such as not knowing how many parts are on the floor. Using a lean system, accidents can be prevented, effort and stress can be minimized, efficiency can be improved, and redundant work can be prevented. The following steps should be implemented:
1. Learn about the key concepts of lean material management.
Before anything else, study the concepts that you need to integrate into your lean material management. Your study should involve a complete research of the different concepts available to you. This way, you can guarantee that you are on the right track.
Concept #1: Avoid an information blizzard.
Today, the phrases “unit-level data” and “real-time” can be seen in nearly every marketing article. People are pushing for visibility and insinuating that real-time information can help you react to events more efficiently and quickly.
Reacting is also referred to as “firefighting.” A genuine lean system develops systems that respond rather than fight fires. Keep in mind that not every piece of information is necessary. You filter out the ones that you truly need in order to come up with effective and favorable decisions. You design a system that gives people the information that they need in order to identify the actions that they need to take. A system that provides directional prompts and is intuitive to use speeds up material transportation while reducing safety-related issues.
Concept #2: Get rid of white space.
All activities have beginnings and endings; this does not mean that every operator’s task must pick up where the previous task left off. A white space exists between these two tasks.
All the processes used in all the industries have five vital steps:
- Queue
- Set up
- Run
- Wait
- Move
Throughout the years, people have focused on the run step of these processes. They focused on running machines, building forecasts, and unloading trucks. They failed to realize that this step is merely value-added. While this step is important, it is not the most wasteful, in fact, the rest of the steps are the most wasteful ones.
To help you understand this concept better, consider the following example:
It is the weekend, so you go to Disneyland. You have heard so many wonderful reviews about it. You see a ride that you like, so you approach it.
The first thing that you do is to wait in line along with other people. – 1. Queue.
After waiting for a few minutes, you reach the front of the line. However, you cannot get on the ride right away because you still must wait for the people on it to get off. You also need to be assisted by the operators. So, you wait for a couple more minutes to get ready to get on the ride. – 2. Set up.
Finally, you can get on the ride and have fun. – 3. Run.
After several minutes of thrill and suspense; the ride is over and you have to get off. However, you cannot just jump off. You must wait for the riders in front of you to get off first. You also must wait for the operators to come and assist you. – 4. Wait.
Once you get off the ride, you can move on to another ride and have a great time. – 5. Move.
If the industrial engineers and managers of Disneyland want to improve the value-added time of visitors, they should not merely focus on speeding up their rides, which represent the step Run. They should also focus on other areas, such as the move, wait, set up, and queue. Placing emphasis on these other areas reduces the time lag associated with material handling. This creates a more efficient system where white space or wait times are reduced to the bare minimum.
Concept #3: Remember that one inch still means transport.
Throughout the years, people have come up with great solutions to transport information and material between companies, over hundreds of miles, and across different time zones.
Loading machines requires manipulation, precision, and articulation while unloading machines merely requires transport. On the other hand, auto-unloading simply requires gravity.
When it comes to designing work stations, your industrial engineers must consider the following alternatives:
- What materials need to be placed at the work station?
- What will the operator/assembler be doing at this work station?
- Should we use gravity/flow racks or a kit-cart set-up for this assembly job?
- How heavy are the materials that need to be unloaded?
Having an optimal layout for your work stations plays an important role in speeding up the factory process. It also reduces the possibility of materials getting damaged when moved.
Concept #4: Get rid of functional tunnel vision.
You should not merely concentrate on good material management solutions. You should also consider contribution material management solutions that can help you serve clients what they need and when they need it, without being wasteful.
With material management, it is crucial for material managers to approach lean transformation with holistic perspectives. Keep in mind that lean was not just created in a day. It is continuously created and re-created all the time. You must learn from past experiences so that you can move on to the next level. Your ability to learn and delete should also be transmitted to the rank and file to ensure everyone is on the same page.
2. Create a Plan for Every Part (PFEP)
You need a database that contains the part numbers that enter the plant, as well as their specifications, storage points, supplier location, supplier, usage, and points of use among other vital details.
First, you need to understand the origins of all the parts. You also need to know where they go and how they are used. With a PFEP system, your data can be centralized. This database or spreadsheet will give you the details of every part. It is useful in managing your material handling system, design timed delivery routes, and storage racks and size markets.
The PFEP can be accessed by anyone in the team. However, only the manager has the authority to input data as well as approve requests for modifying data, particularly if they expand the inventory.
The PFEP database also contains various categories, such as Description, Carrier Transit Time, Delivery Frequency, Order Frequency, Container Type, Supplier City, and Point of Use among others. You must create your own categories depending on the requirements of your business. Collected data can also be leveraged to receive key business insights and automate certain industrial processes.
Want to stay up to date? Subscribe to our newsletter
3. Develop delivery routes for material flow in the plant.
You must design a route that suits your business needs. You must have a sequence that can successfully deliver your parts to the work stations. For example, you can start by marking two-way and one-way aisles for your parts. You can also have a policy that only allows delivery vehicles in the aisles. This way, your material handlers will stick with their schedules.
Choose the most ideal vehicle for your business. Pushcarts, fork trucks, and tuggers are typically available. If you have to transport full pallets, your best option is a tugger train system, which is a train of carts towed in the front by a tugger. Generally, fork trucks are less efficient and are a safety hazard to the operators within the facility.
Next, set the delivery and stop points for material delivery. For example, if you are using tuggers, you should have stop points wherein the tugger driver can easily go to the racks or assembly stations, which are the delivery points.
Build racks at their respective stations. For example, you can use gravity racks to allow your drivers to move containers towards your operators. Your drivers will fill up the racks outside of the stations so that they can avoid distracting the operators.
Assign a specific shelf for every part. Once a container becomes empty, an assembler operator should move it towards the return shelf. It is up to you to decide on the number of containers your racks should contain. Just make sure that you will not have a space problem. Using a flexible and heavy-duty system like the FlexQube concept protects you from having a space problem, as all solutions can be changed to match your flows and materials.
Then, identify your frequency of delivery. Frequent delivery suggests that there are fewer costs and fewer inventories in a system. It also means that there are more system containers as well as more work accomplished by the route operators
4. Use pull signals to integrate your new materials handling system with your information management system.
This ensures that only parts that the stations have consumed are replenished. When you link your information systems and materials, you make sure that only consumed parts get replenished. This link can be made by using a pull signal, such as an empty container or Kanban card.
You may want to go with a decoupled delivery route instead of a coupled route. With the latter, tugger drivers load tuggers in the market and drive them to the stations. With the former, the work gets divided between the drivers (who deliver the parts) and the market attendants, (who load them).
Next, set your standard work for the route operation. For example, you can use standard times to compute how much time is necessary for performing work elements. Be mindful of the speed of the tugger. You need to allow enough time for your driver to get off the tugger, remove a container from the cart, go to the rack, place the container on the rack, get an empty container, use the pull signal, and go back to the tugger.
5. Make sure everyone can efficiently use your new materials handling system.
Everyone, including your industrial engineers, supervisors, operators, market attendants, and drivers, should be able to feel comfortable using the new system. Often, operators, who are used to seeing parts scattered on the floor, experience difficulty in adjusting to new systems.
Those who worry about not having sufficient parts may turn in the pull card before they use the parts in an attempt to create a buffer in the cell. Help your employees learn, understand, and get used to the new system. You also need to make your new policies clear to everybody.
To maintain your new system, supervisors should perform written audits regarding the pull signals, market, and delivery route daily. They must make sure that the new system operates properly. Receiving regular feedback from supervisors will help pinpoint areas of difficulties in order to mitigate them.
6. (Continually) Improve your materials handling system
It is not enough to only develop a functional materials handling system. You also need to make sure that this system is sustained and improved continually. You must perform periodic auditing and daily system monitoring. It is crucial to stay updated with the latest trends in innovations and technology.
For example, your materials handling department should meet every day to discuss problems and find solutions. They should focus on delivery, safety, and productivity. Moreover, your management team should ensure that standard work is followed; and new tools are maintained. See to it that everybody understands that the processes are audited, do not forget to post the results so that everyone can see them.
Ideally, you should begin the implementation with one cell. Once you get a better understanding of the system, you can scale up. Refrain from implementing your system in your entire facility to avoid getting bogged down.
Materials handling is so much more than just handling of inventory. It encompasses a wide range of components that keep the supply chain running. It is not something to be taken lightly. This is particularly true if the materials you move and store are large or heavy. If you are not careful, you can suffer from accidents and monetary losses.
To keep your factory and your business in top shape as well as to avoid lawsuits, you should use lean materials handling to your advantage. You must apply the above steps so that you can prevent accidents, reduce effort and stress, minimize risks, lessen distribution and storage time, avoid unnecessary expenses, and eliminate redundancy. Hire expert workers and have good storage systems.