AGV Case Study: Siemens gets started with automation
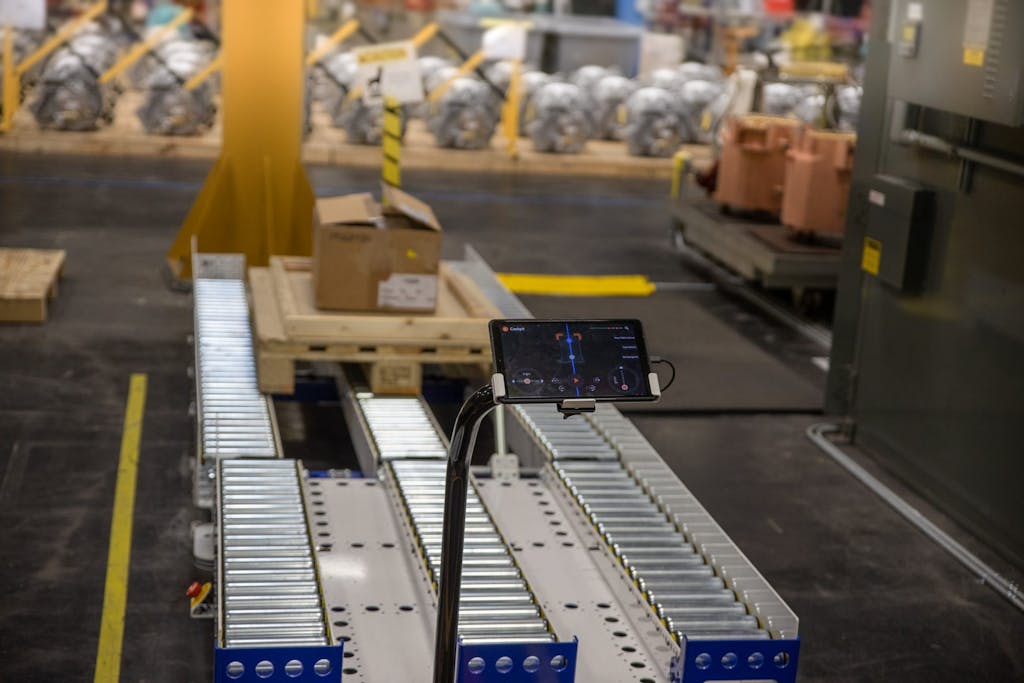
Challenge
This particular Siemens manufactures several different products and recently received several new products to manufacture. These new products needed new processes and new methods of transportation. The previous transportation methods led to movements of the materials to different stations by operators via pallet jack, forklift, or manual pushcart. On top of this, Siemens wanted to keep gearbox technicians at their workstations, eliminating the task of transporting the materials between workstations.
Achievement
FlexQube licensed dealers McGee Storage & Handling, based in Atlanta, introduced the FlexQube team to the Siemens managers. Following this first introduction, FlexQube & McGee were able to present the FlexQube AGV system product to the Siemens team to solve the challenges they were facing. Discussions began about how the AGV could be best used within these processes, what the ROI would be, and the benefits to the system over other solutions. Initial designs were drawn of the AGVs best suited to this project, and virtual testing of the routes completed. Currently, there are two AGVs within the facility, completing several types of transport and removing human interaction throughout the process entirely, leading to 100% automated transports and a short ROI.
Solution
In the end, Siemens needed to opt for two different AGV designs along with a roller transfer station. One was a standard flat deck pallet AGV used for the movement of parts loaded via forklift and then automatically transported throughout the facility. The second AGV was designed with rollers on top, which used gravity to transition the pallets from the AGV to the roller transfer station. A shooter mechanism completed the transfer which mechanically unloaded the pallet from the AGV and transitioned the pallet automatically.
“We got started with a future factory.
We have automation now in our factory, and now we can build on it; we can bring in more robots we can be created and innovative with how we can use this different technology in our factory.”
– Kim Howe, Logistics Manager at Siemens Mobility in Georgia, USA
Siemens got started with automation.
One of the most significant benefits that Siemens could take away from implementing the AGV products into their facility was that they got started. They were able to map out the project, assess their needs, and implement an automation project, which was fully automated. Automation is a journey that will never stop, so taking the first steps can be the most difficult and the most daunting. Still, now those complex steps are over for Siemens.
Robust Automation. Simple Implementation.
When it comes to automation in a manufacturing environment, consistency and robustness are a must. The automation needs to be reliable to turn up and deliver every time, and with the AGV this is assured. Siemens was able to implement a solution that can be depended on every single transport. The AGV also comes without the frustrations of typical automation implementations. The AGVs needed no extra IT infrastructure, and the implementation was completed in a minimal amount of time.