The Benefits of Kitting
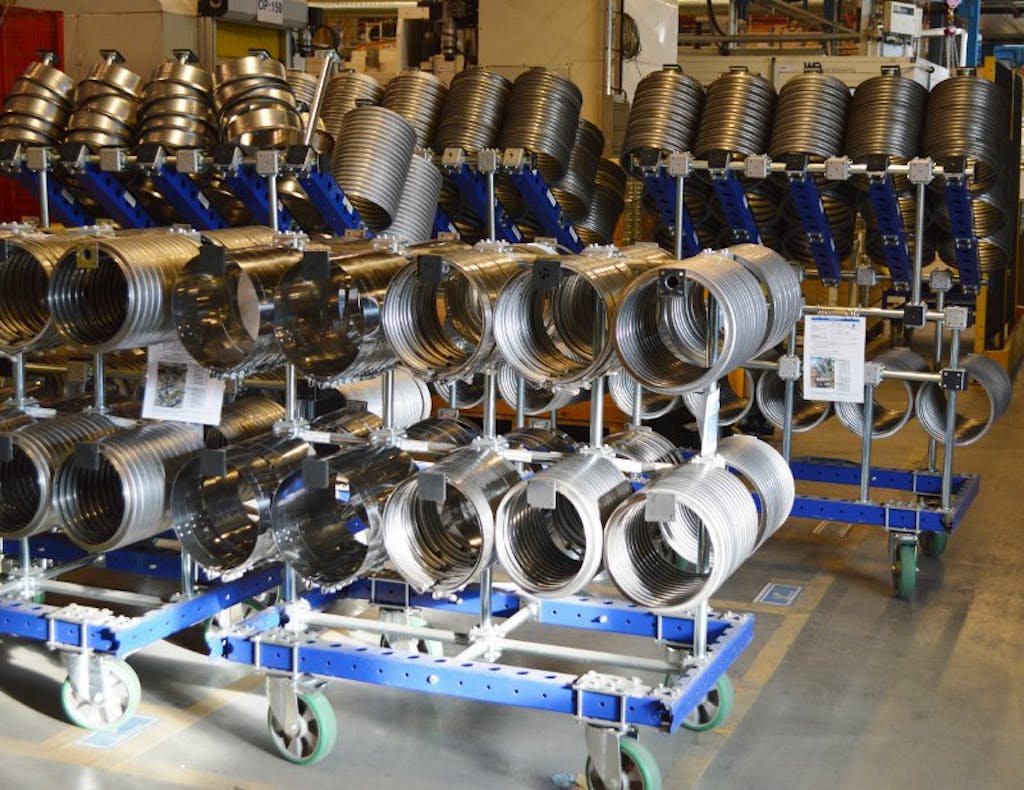
Last Modified: 26/03/2020
As time goes on the global manufacturing market is ever-changing, with a greater number of products, shorter life cycles and an increase in consumers demand greater customization.
The constant pressure to increase the turnaround of new products with a larger number of parts, variants, and components is putting extra strain on all manufacturers. The world of manufacturing and logistics needs to quickly adapt to these demands of the marketplace and the consumer. The ability to manufacture high-quality products while keeping costs low is the formula for success.
However, this is easier said than done with many manufacturing companies losing space, time, and money trying to keep up with the changing trends and demands. One of the biggest unforeseen impacts of this trend towards more products with shorter life cycles and greater customization is the space needed at the line side to store the growing number of components. Due to this realization and the change in space needed to house these components we have seen the emergence and growing popularity of kitting within a manufacturing environment.
WHAT IS KITTING?
Kitting can be defined as the process of gathering parts and components (possibly even pre-assembling some) used in the manufacturing process of a product and delivering the parts to the point of use (line side) in a “kit”. It helps in simplifying the complexity and components at the line side, equipment costs, and boosts efficiency by eliminating “search time”.
Fulfilling different orders by having preassembled groups or kits can be extremely beneficial for the fulfillment of orders or a manufacturing process. The process involves selecting different items that are connected throughout the process and then packaged together as one module. Once the operator receives these preassembled modules they can then assemble them or send them as one unit.
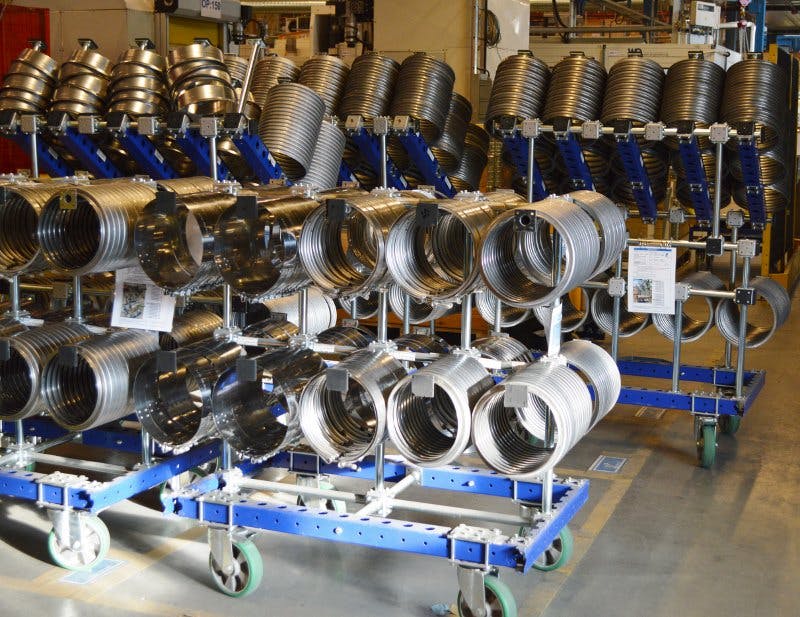
WHAT ARE THE ADVANTAGES TO KITTING?
The expansion in having a larger number of parts and components due to the increase of different variants per product, feeding systems have had to become more efficient. This is the reason why kitting has now gathered in popularity with many manufacturers.
Elimination of “Search Time”
Using kitting as your main material feeding system reduces the time handlers & operators will look for certain parts or components due to all parts arriving within a kit. While this may seem minimal when viewed daily, the time saved monthly or yearly can add up quite quickly.
Improved Organization on the Work Floor
Using a kitting material feeding system reduces the number of parts that need to be available to the operators and handlers on the work floor. This not only improves the organization of the overall warehouse but also improves the safety standards for your workers. Having fewer parts and materials on the factory floor will free up space and therefore reduce the chances of an accident.
Improved Control
So we have mentioned better organization on the shop floor, which in one way, also play a role in the next benefit of kitting in manufacturing – more control over the inventory. Having better control over the inventory is key to achieving an efficient workflow and minimizing quality issues. When kitting, you will never be missing essential components in the assembly. Further, unplanned downtime.
Space
By far, the biggest advantage many manufacturers see in turning towards a kitting system is the space saved at the line side. No more will you have your operators boxed in and surrounded by a wide range of parts and components. Instead, they will have what they need, delivered to them when they need it. The growing trends previously stated (shorter product life cycles, increased product complexity, greater consumer customization) are causing a shortage of space in many work floors today, in particular at the point of assembly. This isn’t an easy challenge for any organization to overcome, so kitting has now become quite common.
While kitting hasn’t been viewed as a solution for every organization it has grown in popularity. The perceived increase in material handling has some organizations a little nervous about introducing a kitting solution. At the same time, some improvements can be made within the kitting method including specially designed kitting boxes or delivery pallets, an improvement in the electronic support and making the kitting locations as close as possible to the line feed, etc.
It does seem kitting will be the preferred method for many manufacturers that are looking at increasing their efficiency, product handling, flexibility, cutting down the complexity at the point of assembly and most importantly creating more space on work floors