Case Study: Autoliv Automotive Components
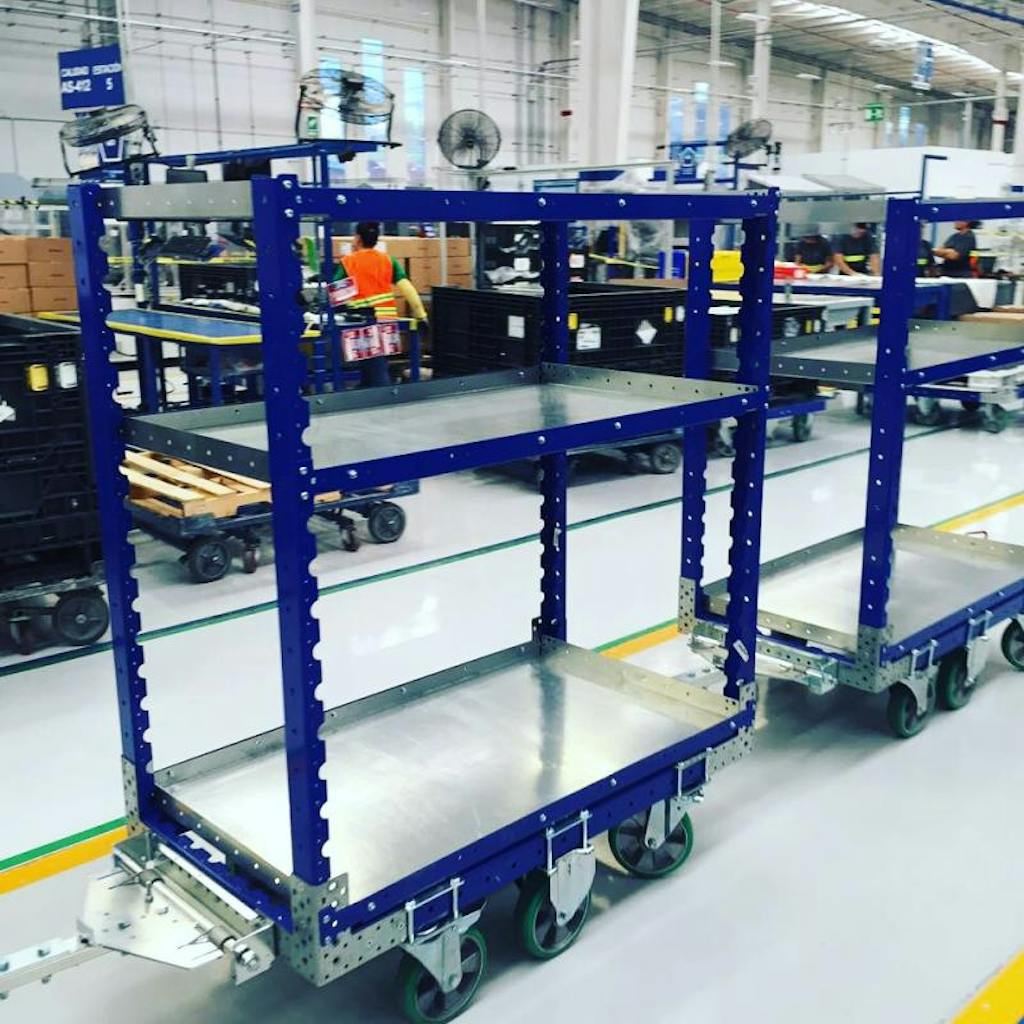
Autoliv purchased many different applications ranging from shelf carts, mother-daughter system (4 in 1) for small boxes and totes as well as container carts for their 48×45 inch containers, 32 x 30 inch containers as well as other more special sized containers. Some 1600 x 1200 mm for example.
The previous system Autoliv was using had quad steer which meant that the carts tracked well behind the tugger but they were very hard to move by hand for the operators. The carts had also very bad casters causing a lot of down time and bumpy and noisy rides around the plant.
FlexQube could offer a modular system in order for Autoliv to be more flexible in terms of creating a cart fleet for the long term. With the FlexQube concept, Autoliv saw a possibility to extend the lifetime of their investment as well as improving their material flow in terms of productivity, environment and quality in the short term.
Since 2015 FlexQube has delivered almost 250 carts to the different Autoliv plants in Mexico with more to come.
CHALLENGE
-
Low quality carts that caused a lot of downtime and maintenance
-
Changes in container sizes due to new demands from OEMs
-
Inefficient material flow
ACHIEVEMENT
-
Increased productivity
-
Reduced noise level in plant
-
One standardized concept in greater quality reduce downtime and complexity
SOLUTION
-
Six caster setup to achieve great tracking and maneuverability
-
Carts more user friendly due to fixed caster in the center
-
Implemented 4 in 1 tugger train system with improved productivity
If you’re looking for a similar solution, contact us at sales@flexqube.com
You may also like:
The benefits of tugger carts in lean manufacturing