Do you have a screw loose?
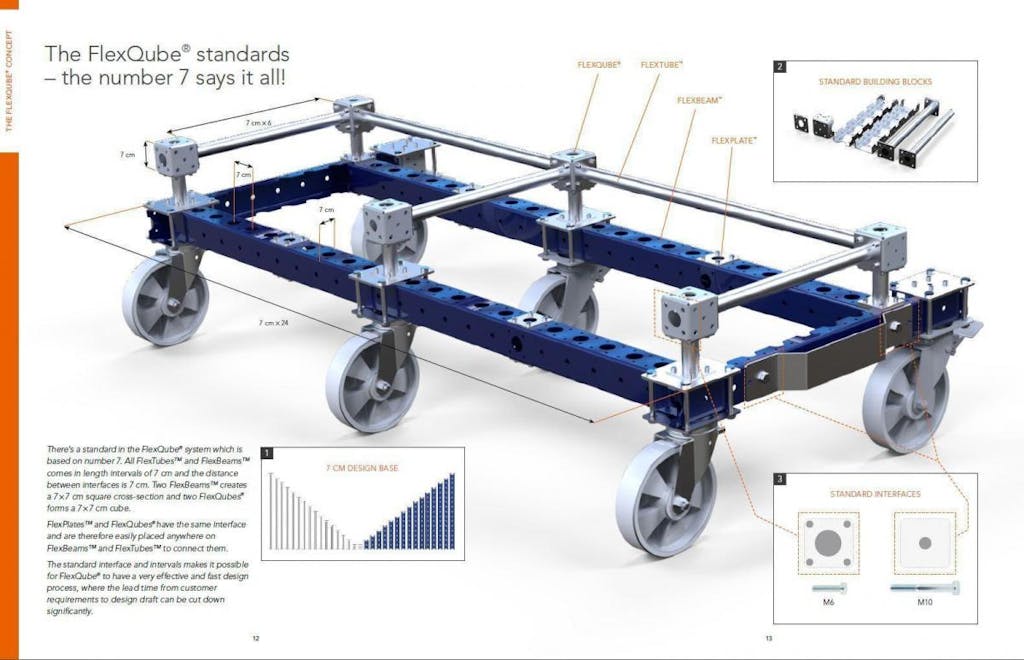
Why don’t you weld the wheels to your car? Because you want to configure the car for different needs, such as summer and winter conditions.
The automotive industry is by far the largest consumer of fasteners and the need is growing. Why is that? Because the car companies want to create different variants of cars. They want to configure cars with different engines, shapes, styles, and performance. They want to produce cars in a more efficient and flexible way and share common materials across many models.
Just as it is obvious why you are bolting the wheels to your car, it’s just as obvious it will be to bolt together your future industrial carts. In fact, I think that today’s industrial carts very much can be compared with a car. The carts get more and more advanced options such as different casters, handles, brakes, sizes, platforms, colors, and integration needs.
Yes, I know that welding is the most proven process to join metal components. The problem is that the process also has so many disadvantages that it soon will be a part of the history books.
Welding is time-consuming and requires fixtures. The heat generated from the welding creates weld distortion that might affect both strength and geometry of the carts. For the operators building the carts, it is a dirty and hazardous process. And most importantly, welded carts are not modular and they cannot be reconfigured. I have visited many factories, and I have seen many attempts to reconfigure welded carts. It doesn’t look very nice, and of course, it is very expensive. In other words, welded carts are not a good investment for the future. Bolted carts are the way forward.
The basic idea with the FlexQube concept is to create customized carts by bolting standardized building blocks together. The carts are robust, easy to design, and they can be reconfigured to meet future needs. If the carts get damaged, it is easy to repair and exchange parts. You can also reduce transport costs and environmental impact by shipping the carts unassembled.
The first known applications for screws can be found during the Bronze Age. They were used in making weapons and jewelry. Thousands of years later the development of screws is still evolving and the automotive and aerospace industry is a strong driver for this. Indeed, the strength and durability of screw joints are nowadays comparable with welded joints.
The FlexQube concept has a well-defined screw standard which consists of M6 and M10 bolts. For example, the M6 bolt is developed in close cooperation with the supplier and uses many technologies from the automotive industry. The screw is creating its own threads, is covered with wax in order to reduce necessary turning torque, and is equipped with a serrated flange in order to secure durability.
If you don’t have a screw loose, visit our Solutions Library™ and get ready for the 21st Century way of building industrial carts.
Qube it!™
Per Augustsson CTO, FlexQube Group