Increasing Throughput Quality by Harnessing Flexible Manufacturing
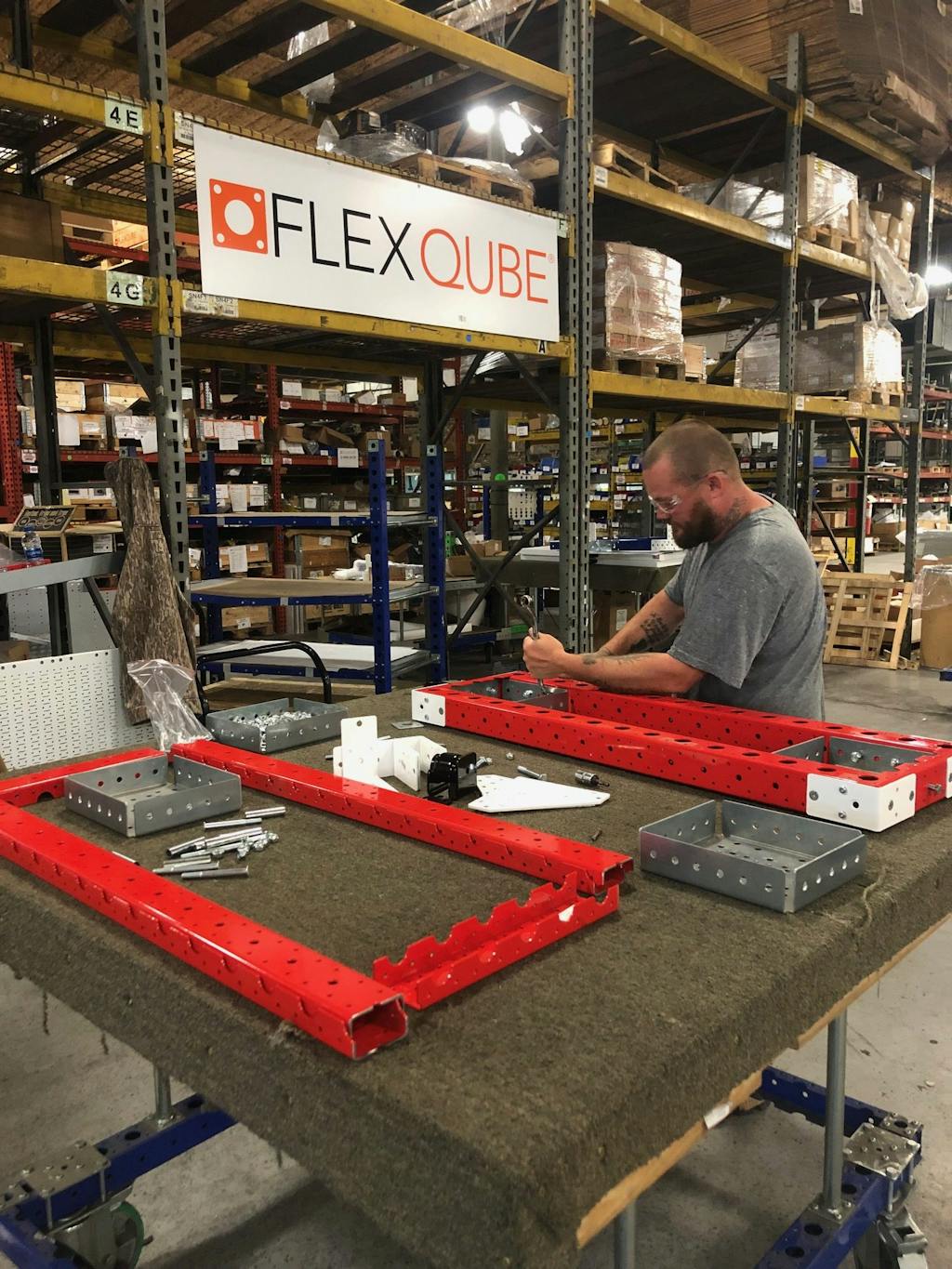
As the public continues to get used to improved service levels from online retailers, industrial manufacturers are increasingly expected to efficiently meet product delivery timelines.
Statistics show that approximately 84% of consumers will not make a second purchase after experiencing poor customer and delivery services, while 98% remain loyal to brands that offer better services.
Now, is probably the time to state that increased service levels start from producing quality products and ensuring enough products are available to meet customer demand. With fluctuating demand circles, a supply chain affected by the pandemic, and increasing government regulations, manufacturers must seek new solutions to navigate the ever-changing manufacturing landscape while improving throughput quality. This is where flexible manufacturing systems (FMS) come into the picture.
A flexible manufacturing system refers to the ability of a production process to quickly adapt to changes in the quantity and type of the product being manufactured. Thus, an optimized FMS must be capable of increasing its production capacity in real-time to meet fluctuating demand without affecting throughput quality. In manufacturing facilities where multiple products or items are produced, the FMS must be capable of responding to diverse order changes and handle changing levels or order of production.
FMS consist of three operating systems that must be controlled to deliver an agile manufacturing process. These systems include the work machines tasked with production, the material handling system tasked with inventory flow, and a centralized computer control system to optimize the production cycle.
Digital Transformation Technologies Enabling Flexible Manufacturing Systems
Although FMS is not a new concept, technological advancements have made its application much easier and implementable today. The digital transformation of the manufacturing industry and its interrelated operations provide accurate insight that supports FMS. One example is the application of demand forecasting technologies to predict future consumer demand, thus setting the stage for agile production.
The implementation of IIoT and the use of computer numerical control equipment enable interconnectivity and the exchange of data across the shop floor. The interconnected shop floor enables the automation of work machines to support FMS. Automated industrial processes bring agility to production cycles and enable shop floor equipment to pivot facility operations when dealing with changing demand cycles.
The digitalization of the material handling process is a crucial aspect of delivering a flexible manufacturing system. Material handling systems handle the flow of raw materials or components across the diverse workstations within the shop floor. Automated guided vehicles (AGVs) and autonomous mobile robots (AMRs) are equipped with the features needed to deliver a flexible material handling system to support flexible manufacturing strategies, and our modular AGV System is specially designed with this in mind. We have a strong belief that a flexible factory is a smart factory. A key enabler for a flexible plant is the industrial carts that transport materials precisely what the FlexQube Concep is all about.
Lastly, digital technologies such as industrial cloud platforms and manufacturing enterprise systems provide the centralized control needed to drive automated assets and deliver a flexible system. The combination of these advanced technologies means implementing flexible manufacturing plans to meet real-time changes and optimize throughput is a lot easier.
Applying Automated Material Handling Solutions to Implement Flexible Manufacturing
Flexible manufacturing requires a flexible material handling system that integrates artificial intelligence to improve its autonomy and flexibility. The main aim of a flexible material handling system is to compensate for the uncertainties within the shop floor. These uncertainties could be caused by increased demand, random machine failure, and inventory management shortfalls.
AGVs provide support for the different types of flexibility in a flexible manufacturing system, such as expansion flexibility, routing flexibility, and production flexibility. Such as when machine failure occurs, an AGV can reroute material transportation to only viable workstations in real-time. For example, with the AGV, you can record multiple routes and easily change how the AGV is navigating throughout your facility whenever necessary, or even change the tape layout in just a couple of hours. The routing flexibility AGVs offer ensures machine failures and other uncertainties do not lead to downtime and the negative effects attached to it.
Expansion flexibility is the area of flexible manufacturing that focuses on the capacity of a manufacturing facility. Expansion flexibility is required to ensure a facility can easily handle increased demand without any effects on product quality. AGVs support expansion flexibility in multiple ways, which reduce operational costs. One scenario is the ease at which its memory can be updated or modified to navigate new pathways in real-time. Another example is the ability to attach multiple tugger carts or pallets to AGVs to increase their load-carrying capacity to meet increased manufacturing capacity.
Production flexibility is also an important aspect of a flexible manufacturing system where multiple products or components are being produced within a factory floor. Workstations in product-flexible facilities are equipped with machines capable of handling multiple tasks and must be provided with diverse tools and materials to work with. AGVs support the application of production flexibility by automating the material handling process required to transport varying materials or tools to flexible workstations.
AGVs also serve as temporary storages to support just-in-time deliveries within FMS facilities. Without manual aid, AGVs can wait in a queue holding specific items within a distance of a workstation until the items are required. The AGVs’ ability to automate the queuing and just-in-time delivery process leads to improved machine utilization and increased productivity or throughput quality.
The safety aspect AGVs bring to flexible manufacturing systems with increased floor traffic cannot be overlooked. AGVs are equipped with safety features such as collision detection mechanisms. The AGV System is equipped with high-quality scanners that create a 360º view with no blind spots.
Conclusion
AGVs ensure the implementation of a vital aspect of a flexible manufacturing system which is automating the material handling process. An automated material handling system with the capacity to handle expanding manufacturing requirements and react in real-time supports FMS which leads to increased throughput quality regardless of the uncertainties surrounding the production process. Increased throughput quality and meeting delivery timelines lead to improved service levels and customer loyalty.
If you are interested in implementing more flexible manufacturing, please reach out to our experts and book a meeting to learn more about how you can harness flexible manufacturing and its benefits.