Innovative intralogistics is a main enabler for Lean Production!
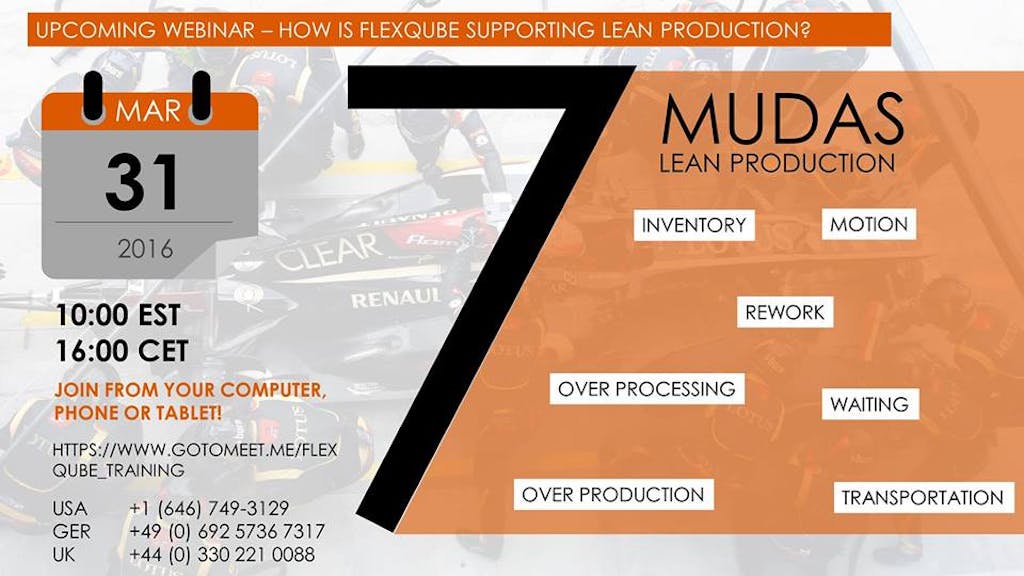
Learn how the FlexQube® concept supports the principles of lean production in the upcoming webinar on March 31st.
The Lean production philosophy has been established for a while, and it derives from Toyota Production System that is the most well known production system all categories. The main objective with the philosophy is to eliminate waste. Lean is a war on waste. Any activity that does not bring any value to the customer is considered as waste. If customers are not willing to pay it, it should be eliminated! Below are seven type of wastes to consider.
1. Overproduction
Production ahead of demand
2. Inventory
Components, work in process and finished product not being processed
3. Transportation
Unnecessary movement of products and parts
4. Motion
Unnecessary movement of people
5. Waiting
Waiting for the next step in the process
6. Over processing
Resulting from poor tool or product design creating activity
7. Defects
The effort involved in inspecting for and fixing defects
Smart solutions can reduce a lot of waste within the intralogistic process itself. But even more important, smart intralogistic solutions has a major impact on reducing waste for the next step (customer) in the process.
A typical customer of the intralogistic process is the assemblers. The assembler puts all parts together into a final product. That’s what it is all about, putting parts together and create value for the customer. Though, putting parts together has become more and more complex as companies offers more and more products to their customers. This variation ends up in the hands of the assemblers. They are responsible for building all the different products, often on the same assembly line.
The logistics process has become the main enabler to support the assemblers handling the increased complexity, and in the same way reduce waste. Let´s take one example, the travelling kit!
A kit is a set of parts that is dedicated for a specific station, a specific operation and a specific assembler. The parts are loaded on a cart in a preparation area located in-house or at the supplier.
Designing the kit cart in the right way will have big impact on reducing waste for the assembler!
1. The cart itself can be the assembly instruction. The parts should be placed on the kit cart with the same orientation as used for assembly on the final product. In addition, also the the assembly sequence can be visualized on the cart.
2. Place parts in ergonomic height. Picking in ergonomic height is fast and it will reduce injuries.
3. Let the cart follow the the assembler. By attaching the kit cart to the product or the conveyor during assembly the walking distance will be significantly reduced.
4. Split carts. If there are several assemblers on a station create a kit cart for each assembler. This is perfect to combine with a mother daughter train delivering all carts at the same time.
Click here to read about the previous webinar on Forklift free production.
/Qube it!™
Per Augustsson CTO, FlexQube®