The 5 Challenges to AGV Implementation and How to Overcome Them
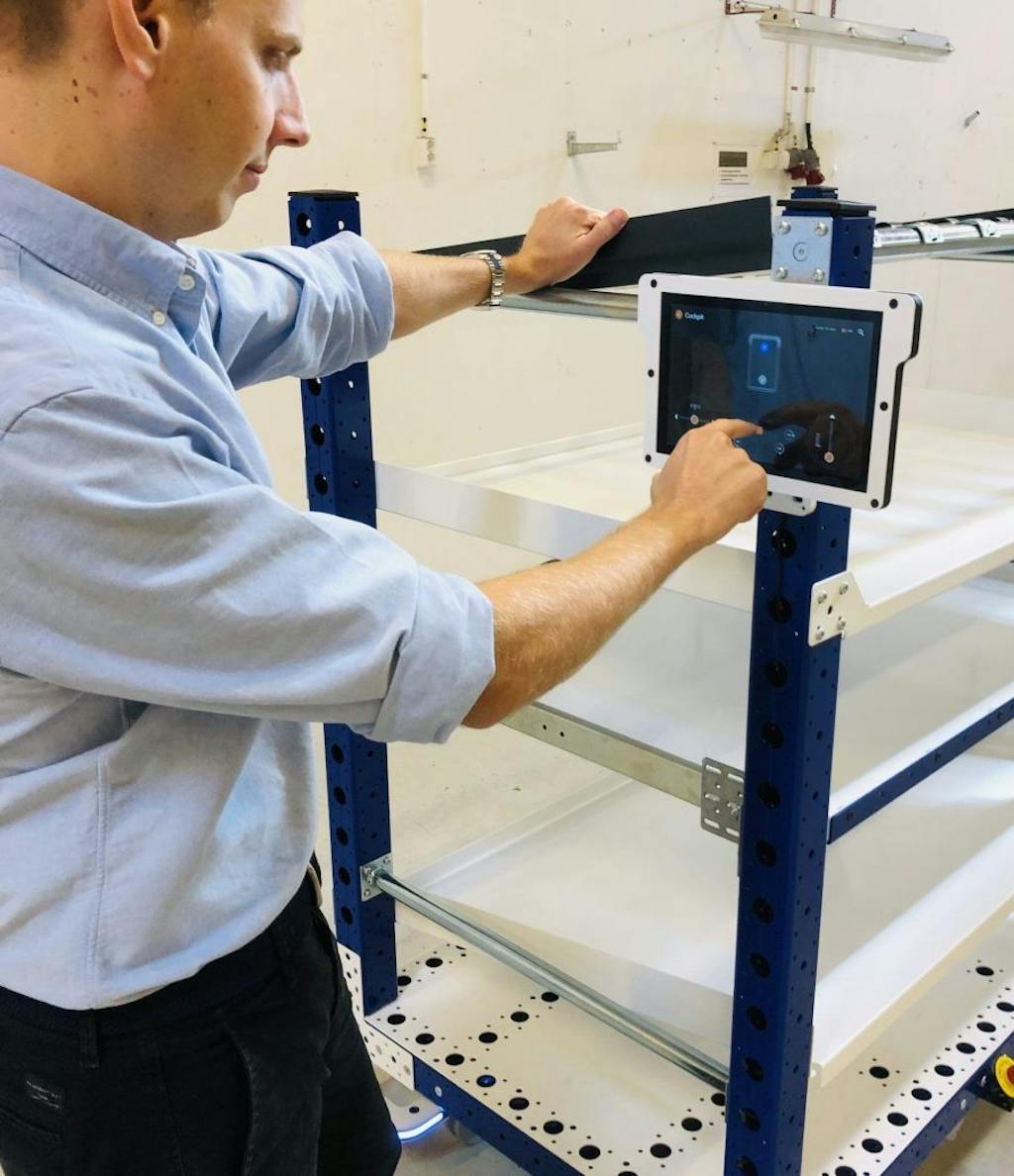
Facility owners using or considering the use of automated guided vehicles (AGV) for material handling.
This is the result of the integration of lean manufacturing and the increasing adoption of Industry 4.0 in warehouses and manufacturing shop floors. In terms of implementing AGVs, there are a couple of common challenges facility owners must navigate through to achieve perfect implementation and optimized business operations. This article will cover:
- The top challenges to implementing AGVs
- Why these challenges must be solved and
- The solution to these challenges.
Top 5 Challenges to Implementing AGVs
1. Plant Layout Challenges
In most warehouses, shop floors or manufacturing facilities, still, make use of legacy material handling equipment such as forklifts and hand carts to move materials around. Thus, the first challenge is converting older navigation lanes to pathways conducive for AGVs.
If this is a challenge you face, the solution to it is re-organizing your shop floor to support both the passage of traditional material handling equipment and AGVs. The AGV lane should be able to manage traffic and alert workers about any potential overlaps or crisscrossing traffic.
2. Fleet Management Issues
AGVs are designed to have a map of your current factory floor to successfully navigate through walls and objects obstructing its part. This is made possible by in-built sensors, scanning, and mapping features. The AGV sensors scan solid objects which means they see storage racks with legs as legs with passable passages, not walls. This means the AGV might attempt to pass under a rack when navigating the shop floor.
To properly manage a fleet of AGVs without incurring losses due to accidents, the AGV needs to be programmed to recognize rack legs. If this fails, low walls should be added to the rack legs which will create an effective illusion of walls to the AGV.
3. Dealing with Speed and Movement Limitations
The speed at which AGVs move, their degrees of freedom, the ability to drive in reverse, and the turn radius is determined by the manufacturer. Therefore, the ability to deal with reverse driving and turning may be limited to the AGV you use. In some cases, AGVs without rear-facing sensors are slower when moving in reverse. To eliminate these challenges, purchasing AGVs with rear-facing sensors and zero-turn radius allows for quicker reversals and tighter maneuvers. A cheaper alternative involves managing the speed limit so AGVs do not travel at faster speeds and arranging payload pick-ups and drop-offs to optimize navigation can help.
4. Dealing with the Possibility of Collisions
It is important for facility owners to know that AGVs cannot flee and understand what this means. AGVs react to head-on collisions with forklifts or carts by stopping in its track and finding alternative routes to bypass collisions. This means accidents are bound to happen anytime an AVG’s lane witnesses fast-paced traffic from other material handling equipment.
To limit the possibility of collisions occurring, ensure that forklifts and AGVs do not have similar navigation layouts or pathways. This eliminates the possibility of these two material handling equipment coming in contact with one another. In situations where different types of material handling equipment must be used, smart carts or AGVs should be used. These AGVs are equipped with optical cameras, motors, and microprocessors for navigation purposes.
5. Understanding the Total Cost of Ownership
Choosing to integrate AGVs in your facility can be an expensive project to undertake. Facility owners must know the true cost of ownership before taking the step to purchase this material handling equipment. The true cost of ownership must include calculations on power use for charging AGVs, cost of re-orientating the layout and purchasing the tech solutions needed to collect data and manage operations.
These overlapping payments are part of the reasons why AGVs are used by big corporations such as Amazon and Ali Express. If the returns on investing in AGVs do not meet your financial permutations, choosing to use modular carts or AGVs are flexible and more affordable options to use.
The Way Forward
Autonomous vehicles will become fixtures soon. Innovative companies are currently exploring ways to integrate AGVs as replacements or complementary solutions for handling materials. The integration process will come with its challenges and this is where experienced hands are needed. You can learn more about your material handling options for your smart factory by speaking with an experienced engineer at FlexQube.