The Material Handling Guide to Implementing Industry 4.0 Concepts
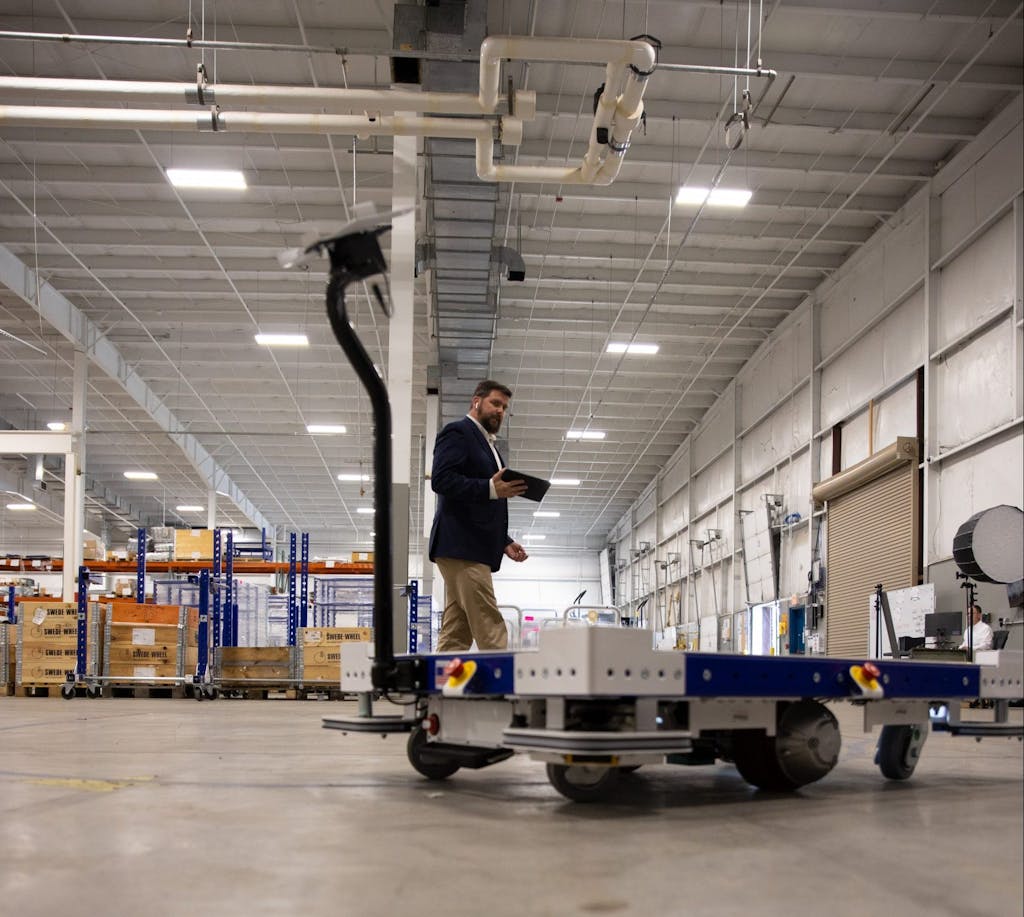
Since its inception by the German industrial workgroup in 2011, the fourth industrial revolution has continued to advance manufacturing and industrial processes exponentially.
The application of digital transformation technologies within the industrial sector is expected to lead to a 6% increase in global productivity, which is more than was accomplished two decades ago.
The current successes in applying Industry 4.0 business models have been achieved through considerable technological advancement and their application in today’s smart factory. Edge computing, industrial IoT, and the digital twin are quickly becoming household names in the industrial sector. This is due to their ability to capture and support the interexchange of data, but many overlook another crucial factor to implementing the industry 4.0 concept – a digitized material handling system.
Every facility manager and operator knows the important roles efficient material handling processes play in greasing the wheels of production cycles.
Here, you will find the information you require to kick-start the digital transformation of your material handling system.
Is an AGV or AMR the Best Option for Your Facility?
The first step to implementing a digitally transformed material handling system that delivers automation is gaining knowledge of your options. Today, automated guided vehicle systems (AGVs) and autonomous mobile robots (AMRs) are the two material handling solutions known for their ability to support industry 4.0 business models. Both options capture data, rely on data to navigate the shop floor and can navigate unstructured space.
This leads to the question, which option is perfect for your industry 4.0 applications?
The short answer is that AGV and AMRs are both automated material handling systems. The longer answer involves analyzing the operational mechanics both options employ, the total cost of ownership, and the support they provide for Industry 4.0 applications.
AGVs are intelligent robots that utilize sensors and a defined route to navigate the factory floor and avoid obstacles. AGVs rely on tape, magnetic, or beacon-equipped paths to navigate shop floor layouts. The robot, in turn, moves along or tracks its movement through lasers, magnets, vision cameras, or radio waves.
AMRs are basically advanced versions of AGVs. The AMR is equipped with advanced sensors and data capture and processing technologies to execute its duties. AMRs take a smart, dynamic approach to navigate factory floors by planning their path, recognizing obstacles, and collecting data along the way.
Finally, choosing between both options should be decided by what you intend to achieve with an automated material handling process and your needs. Thoroughly investigate the specs and limitations of the project. It is a good idea to determine what would be nice to have as opposed to what you need to have. Furthermore, you need to consider what load you will be transporting and your existing layout and procedures.
5 Steps to Implementing Automated Material Handling Systems to Optimize Industry 4.0 Models
Like all industrial automation implementations, implementing an automated material handling system starts with creating an implementation plan to guide the entire process. The 5 Steps to implementation include:
01. Developing an Implementation Blueprint
Implementation blueprints must be clear on what the automated material handling system intends to achieve when supporting industry 4.0 business models. The blueprint must consider the facility layout and the effect of the implementation process to convince C-suite decision-makers to go ahead with it. The following questions can help with designing a comprehensive implementation blueprint:
- What does the automated material handling system intend to achieve? Is it improving safety, providing support for data-driven policies, or improve productivity?
- How will the automated material handling system be integrated into our existing facility?
- What technology solutions will we require to implement a high-performing automated material handling system?
02. Seeking Out a Technology Partner
The manufacturing or warehousing professional’s expertise revolves around improving productivity. The process of designing and installing some AGVs or AMRs requires another type of expertise that only an automated material handling service provider can provide. 7 out of 10 more complex DIY IoT implementations fail and implementing an automated material handling system falls under this category. The following questions can help with choosing the right technology partner:
- What automation process do you use, how does it work, and what is the onboarding process like?
- We would like an automated material handling system with custom-built AGVs, can you develop this?
- What clients in our niche have you worked with, and can you put together a demo workshop for us?
03. Determining Total Cost of Ownership
Purchasing and installing an automated material handling system does not mean your expenses end there. To keep an automated material handling system running optimally, regular maintenance, updates, and performance monitoring are required. The average AGV or AMR also consumes its fair share of energy which must also be factored into the equation. These expected expenses make up the total cost of owning an automated material handling system.
04. Compatibility with Industry 4.0 Business Models
An excellent implementation blueprint must consider how an automated material handling system supports industry 4.0 initiatives but shouldn’t stop there. The material handling system to be developed must be compatible with existing or new technologies and shop floor assets to function optimally. These assets include digital transformation solutions like inventory management software and legacy workstations where materials will be delivered to.
05. After-sales Support
Implementing an automated material handling process is the first phase of ownership. With time, certain components may require technical updates or your specific requirements may change. This is where the technical support a solution provider provides come into play. After-sales services include updating routes and helping your facility navigate through capacity expansions, maintenance, and technical failures.
Conclusion.
Industrial automation is a crucial aspect of Industry 4.0, and an automated material handling system provides the support needed to develop a smart manufacturing facility. Starting the automation process with the right partner is crucial to the success of your implementation plans.
You can speak with an expert today to explore how AGVs and AMRs can optimize your industry 4.0 business models.