Top 5 Benefits of Gravity Flow Racks in Manufacturing
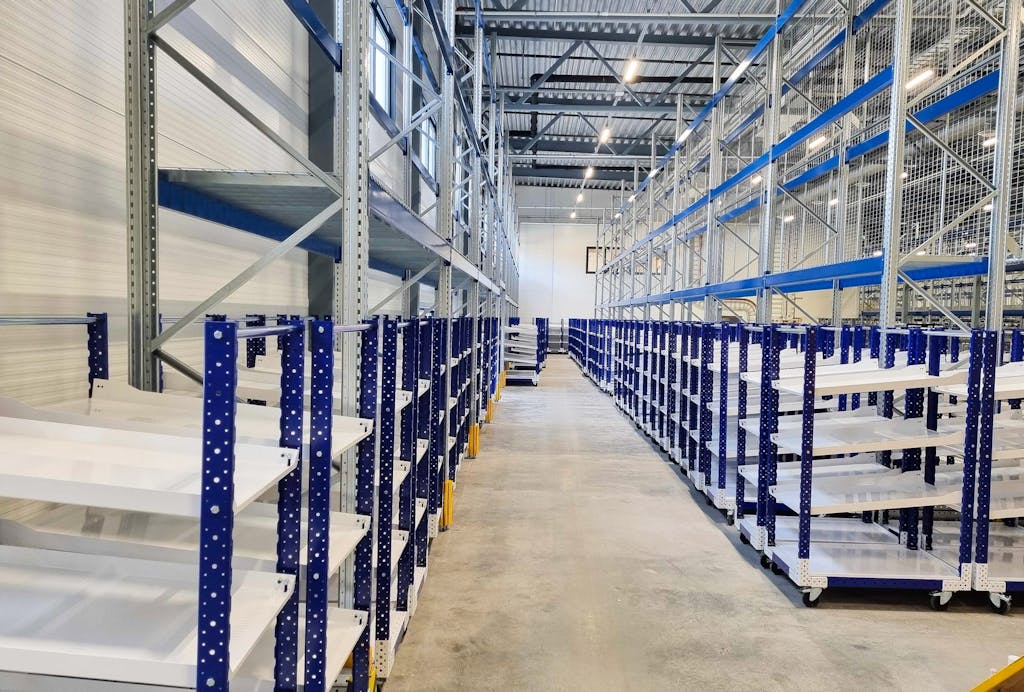
Effective inventory management is crucial to optimizing production runs across every manufacturing shop floor. When executing either short production runs or large-volume work orders, ensuring technicians are provided with the required tools and materials improves productivity by approximately 15%. Gravity flow racks enable manufacturing facilities to implement just-in-time material delivery strategies that guarantee optimized productivity.
Analyzing the Gravity Flow Rack Process
As its name suggests, gravity is central to how this unique material handling system works. Gravity flow racks leverage gravity to move inventory to the front position thus providing quick access to required inventory at need. The working process involves the placing of inventory within the loading side of the system and when the front-most item is picked, the next item moves to the pole position. The sequential order in which every item glides is executed by the pull of gravity.
The sequential order of the flow system may be accomplished in two ways – First-in, First-out (FIFO) and Last-in, First-out (LIFO) process. For FIFO, the first item loaded into the gravity flow rack is picked first and for LIFO, the reverse is the case.
The Benefits of Utilizing Gravity Flow Racks
Reduced Operational Costs – Conventional electric-powered racks such as pallet shuttles are generally powered by electricity to move items through the system. Gravity flow racks, well, rely on gravity which is free. This drastically reduces the operational cost of managing inventory. Electric-powered options also require continuous maintenance to ensure they function properly, and this isn’t the case for gravity flow racks.
The low-cost maintenance and utilization processes associated with gravity flow racks reduces their operational costs when compared to electric-powered systems. The innovative use of gravity makes it more efficient than selective racks that utilize forklifts to stock their aisles.
Optimizes Shopfloor Spaces – Eliminating shop floor traffic by maximizing space improves safety and productivity within manufacturing facilities. Gravity flow racks offer higher density compared to static material handling systems because they do not require as many aisles. They achieve higher density by successfully incorporating up to 12 pallets spread across two aisles.
The reduced aisle space and choice of multiple pallets support stocking many items that are accessible to technicians on the shop floor. Selective racks and other systems require more aisles thereby taking up more space.
Supports Modular Integration with other Rack Systems – Warehouses and manufacturing that utilize extensive rack systems generally execute these systems using diverse types of racks. Rack systems are configured to satisfy a diverse range of specific picking requirements and the modular configuration of the gravity flow rack supports these systems.
Modular rack systems support just-in-time inventory management initiatives and reduce crowding on the shop floor. Thus, improving operational efficiency and reducing operational costs.
Easy Configuration and Design Flexibility – Gravity flow racks do not utilize complex electronic components and wiring that makes configuration difficult. Its modular construction or design allows manufacturers to configure and modify gravity flow racks into diverse functional systems. Configuration and modification are executed using everyday tools which also simplifies the process.
Enables the Easy Tracking of Inventory – Keeping track of available inventory is crucial to monitoring material availability and dealing with stock outs. Gravity flow racks enable manufacturers to track the available inventory on the shop floor and provide more when required to ensure an adequate flow of resources.
Your Gravity Flow Rack Options
There are different types of flow racks you can take advantage of to optimize your inventory management processes and reduce manufacturing costs. Examples include:
- The Standard Flow Rack: The flow rack is equipped with multiple shelves and enables you to increase its shelf capacity at need. The standard flow rack can be used to execute your FIFO or LIFO material handling system.
- Tugger Flow Rack: The tugger flow rack is equipped with tires to enable easy attachment to automated or driven vehicles for transportation across the shop floor.
- Modular Flow Rack with Roller Shelves: This modular flow rack is built with roller shelves to increase its loading capacity and maneuvrability across shop floors. The outlined gravity flow racks can all be integrated into your existing material handling systems with ease.
Gravity flow racks can be the inventory management game-changers you need to revamp your manufacturing processes to achieve optimization. You can learn more about kickstarting your turnkey systems or enhancing existing material handling systems by speaking to a FlexQube expert today.