Why is the AGV the most user-friendly automation solution on the market?
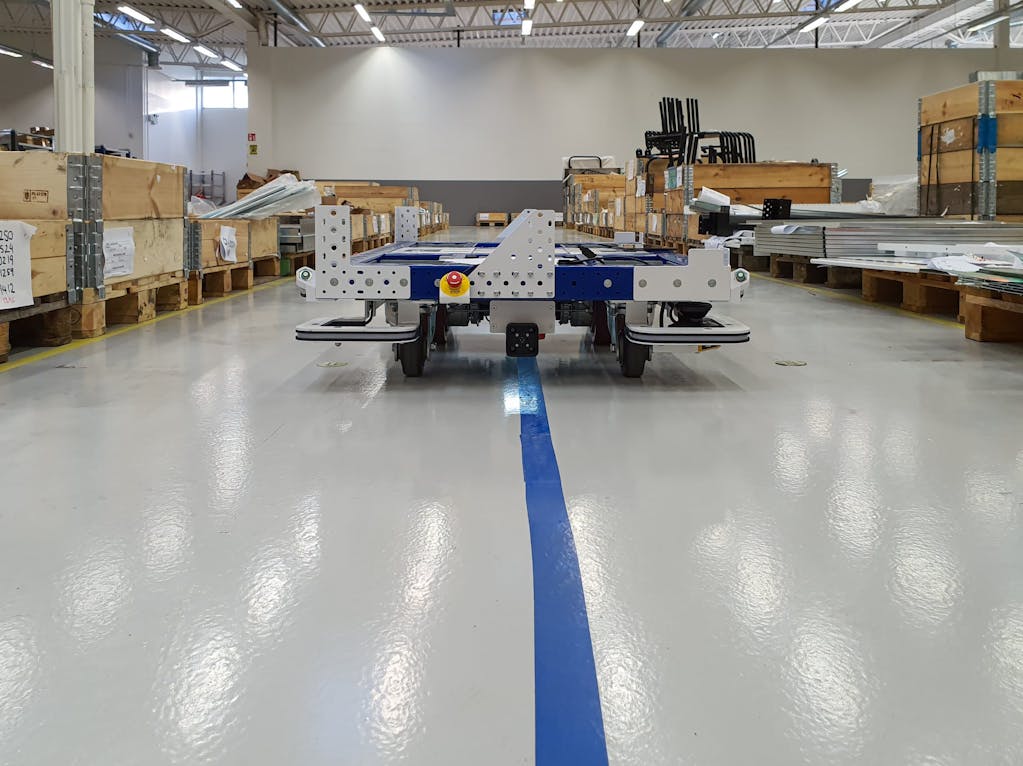
Since coming to the market at the beginning of 2020, the AGV has shown that it is one of the most straightforward and user-friendly automation solutions out.
Compared to other automation solutions, the speed that operators and engineers can familiarise themselves with the AGV has been impressive. From the beginning, the FlexQube R & D team has had ease of use and simplicity as some of the most critical factors in the AGVdevelopment. Factors such as a simpler navigation method, ensuring that there is no integration needed and a user-friendly interface have led to the AGV being the simplest automation solution on the market.
Simple navigation
Initially, it can be seen that having simple navigation technology could be negative; however, it is, in practicality, a big positive. When discussing the implementation and integration of automation solutions with manufacturing engineers, a common thread about complexity is always brought up. The complexity that comes with implementing an automation solution with advanced navigation technology is immense. In our recent Industrial Automation Survey, where we surveyed manufacturing engineers from around the globe, 33.3% stated that implementation constraints were one of the significant challenges being faced in the adoption of automation.
The AGV looks to solves this pain point by using a more straightforward approach to automation. The AGV might not always automate your whole process 100%, but it will automate 80% of the process. When engineers break down the necessity of their automation project and outline the fundamental movements and transports that need to be automated, generally 80% automation is enough to drive greater efficiency, safety, and overall improvements. The AGV navigates optically using a camera installed with a dual side fish eye camera and only requires a contrast on the floor to follow. Most commonly in AGV installations, tape has been used as the primary form of navigation. This is because of the high level of flexibility that comes with having a route that you can easily change and edit how you like.
Looking for some general AGV info? Ask here
Short and easy implementation time
Using simpler navigation technology leads to a shorter and easier implementation time. Having an automation solution that can be rolled out of its box and a route set-up in under 2 hours allows AGV users to receive feedback instantaneously. The AGV implementation process’s simplicity cannot be understated; below, you can see the total number of steps involved in the process:
- Open the box and remove the AGV.
- Plan your initial route and begin laying the tape.
- Ensure the tablet is connected to the AGV and open up the AGV cockpit application.
- Drive the AGV over the tape on the route you have set-up.
- Set the AGV to the mapping function in the tablet and begin mapping.
- The AGV is now ready for industrial use.
27.27% of manufacturing engineers responded in our industrial automation survey that skilled labor constraints were an issue in adopting automation solutions. When comparing the implementation time of the AGV to the demands of other automation solutions, the value of having such an easy implementation is remarkable.
User-Friendly Interface
The AGV cockpit has been designed with the operators in mind. Each AGV is delivered with a tablet, which is used as the main driving and interaction unit. This is so that each AGV can be communicated within a simple and easy to understand way. Tablets and applications have become everyday use, and most employees understand how to use them with ease. This lowers the barrier between the AGV and your operators, as operators can easily use the tablet to communicate and give commands to the AGV. Compared to other automation solutions on the market, operators have limited options in communicating with the robot. This increases the barrier between robot and operator, moving further away from user-friendliness and simplicity.
The AGv was designed from day one as a solution that will become the easiest to use automation solution on the market. While it may not automate entire processes, it is evident that this is not all automation projects’ goal today. 76.92% of respondents in the industrial automation survey stated that improving efficiency is the number one reason for implementing an automation solution. Implementing the AGV will lead to an improvement in efficiency without implementation or integration headaches that come with other solutions on the market.