Is Your Manufacturing Line Ready for A Tugger Train System?
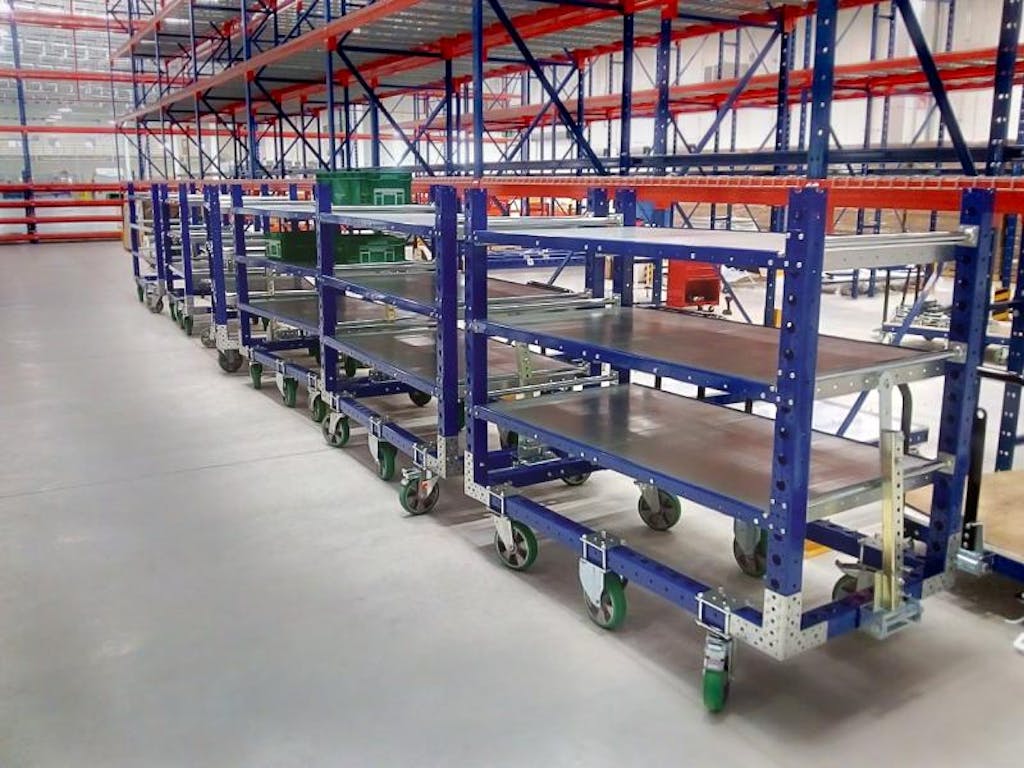
Every time you research, search or browse about Tugger trains and Tugger carts, all you discover is how forklifts are dangerous and statistics showing the death-count due to forklifts. This information is also quickly followed by ‘use a Tugger cart to limit the deaths.’ Almost no one bothers to help you answer the question about your manufacturing line’s readiness for a Tugger train system. This is why in today’s post; the value-added proposition of a Tugger line system and how to get your shop floor Tugger cart-ready will be the focus.
Starting with a simple definition, Tugger trains are material handling and transportation equipment that consist of an automotive vehicle with multiple material handling carts attached to it. The carts can be customized to hold different types of materials while a single rider drives the vehicle. As you can see, Tugger trains are basically in-house commodity trains, and like all freight trains, a transportation pathway must be created for smooth movement. And the Tugger carts, Train line, and routes are what make a Tugger train system.
Assessing Your Manufacturing Line and its Material Handling Requirements
The target of every efficient manufacturer is to produce quality goods without wastage and according to a set duration. To achieve this, your shop floor layout, machines, and material handling equipment are chosen to optimize production. But if you are not meeting set targets due to delays that feel like unforeseen circumstances. This means it is time to evaluate how materials are handled and transported across your factory.
Also, if your assessment shows that many raw materials end up damaged or defective, before getting to their appropriate station, this categorically means you must reconsider your material handling and transportation approach…and as expected, this is where Tugger train systems have a role to play.
What You Should Know when Planning for A Tugger Train System
First and foremost, it is important to note that the planning and implementation process will take time. As stated earlier, Tugger trains require a customized route or pathway that will accommodate its movement and delivery pattern. Other important things you should know include the following:
1. Type of Carts – When talking about carts, there are multiple cart options to choose from, and if you are involved in discrete manufacturing you can even choose to customise your carts. Therefore, when considering the carts that will make up your train, the type of materials you intend to handle and transport should be the guiding light in your decision-making process.
2. Length of Train and Vehicle Power– Another important consideration to keep in mind is the length of the train you intend to work with. In order to make this decision, the factors to consider include the layout or available space in the factory. The tugger train you use must be able to fit and easily navigate the spaces in the factory. The second consideration is the power of the vehicle that will spearhead the train, and this can be determined by assessing the weight of the materials to be carried. It is essential that the right cart is used to transport your materials to avoid the train breaking down in-between transportation jobs.
3. Process Times – Process times are the time durations spent loading, driving, and unloading. Therefore, consideration must be given to the type of loading and fastening equipment integrated into the cart. When considering driving times, the power of the driving vehicle, driving routes and expected delivery times must be considered. Lastly, unloading the materials carried in the train must also be done efficiently to eliminate the risk of damaging the goods. Therefore, the fastening equipment or device used must also be easy to unfasten.
4. Assess the ROI – Every business decision is taken after considering the returns on investments made. Therefore, your plans must include staff earnings, the cost of setting up the system and the benefits of integrating a tugger line system in your manufacturing lines.
You can contact us today, if you are interested in starting the assessment and planning process for your own tugger line system at sales@flexqube.com
You may also like:
4 steps to adapting your manufacturing lines to change
How to start the transition from forklifts to a tugger train system